The most suitable hairstyle for women over 60 can be the decisive element in boosting their self-esteem and improving their appearance. This post discusses spectacular layered hairstyles for elderly women over 60. Layered hairstyles are popular for their numerous styling options, face-framing capabilities, volumetric features, and texturing of aging hair. This post will focus on beautiful layered styles of different hair types, face shapes, and personal preferences. From classic short layered styles to longer styles that fall gracefully to the shoulders, we strive to provide helpful information for selection and embody ageless elegance and beauty.Find more info now
What are the most flattering layered haircuts for women over 60?
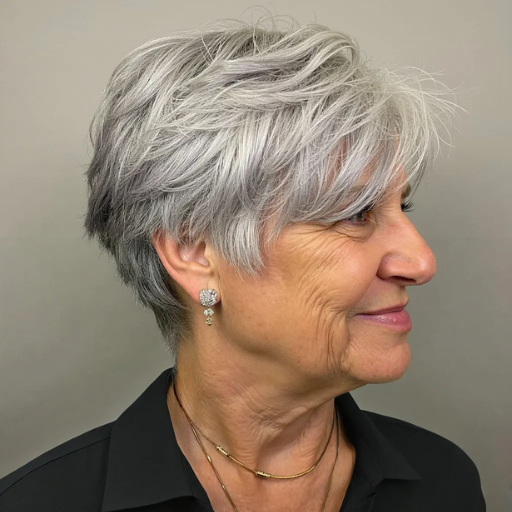
Layered haircuts for women over 60 are practical, stylish, and trim for work. A soft, preppy haircut with calico layers creates an effortless and clean look that is easy to maintain. If you prefer longer styles, a bob to the chin with layers can flaunt elegance and enhance facial features. Shoulder-length layered cuts are ideal for style as the hair moves naturally and bounces around, making it appear lively and vibrant. An additional set of bangs, perhaps wispy or side-swept, help highlight the eyes by framing an aged face. All while preserving their natural features. These looks help to put forward beauty and adaptability for all women over 60 and elevate their confidence.
How do layers enhance hairstyles for older women?
You can also add a bang to the older person’s head because the layers help soften the sharp edges of the aged person’s face while adding adaptability to the appearance. It also increases their softer hair’s volume, texture, and curls. You could style it any way you liked to elevate your appearance. Off-the-head hair condensing onto the nape can also aid in changing the look alongside lengths, proving themselves versatile on different occasions. As long as the right cuts accompany the hair, it will instantly look polished. So, while the less dense hair lacks and the voluminous hair is soft with low density, every woman can adjust to their unique texture.
Which face shapes benefit most from layered hairstyles?
After doing some research, I believe layered hairstyles can suit a variety of face shapes. A layered hairstyle can provide additional definition and depth without disrupting the proportions of an oval face. A chin-length or chin-length hairstyle can give length and definition to a round face. A square face will look softer and more rounded when enhanced with a layered hairstyle, wildly when styled with elongated or tapered ends. A heart-shaped face is better suited to layered hairstyles that can add width to the jawline and soften the look around the chin. Overall, adjustable layers can complement almost any face shape.
Are there low-maintenance layered options for women over 60?
And yes, there are practical yet stylish, low-maintenance layered options for women over 60. A long-styled pixie cut with soft layers is an ideal pick. It is easy to manage while adding texture. Another practical shoulder-length layered bob remains chic—its gentle movement provides an effortless style. For women with natural waves and curls, choosing layers that work with the hair texture saves considerable styling time. The above-quoted styles bring thought to the table while catering to age appropriateness.
How can layered hairstyles make thin or fine hair appear fuller?
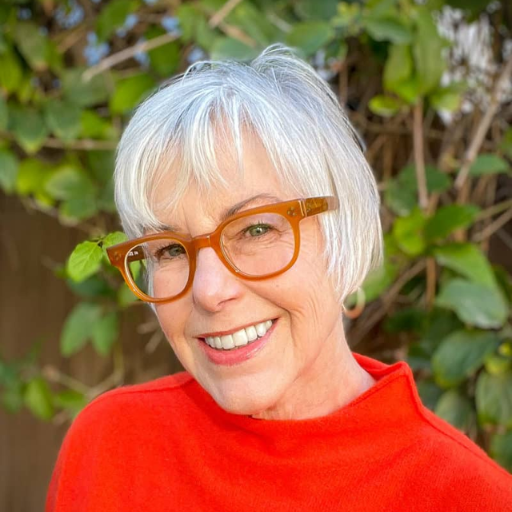
Due to the added movement and volume, layered hairstyles help create the illusion of fuller hair. Layers can also produce lift, making flat hair look fuller. Texturizing techniques and layers give the hair fuller shapes, wildly when styled with volumizing products.
What layering techniques create the illusion of thicker hair?
Techniques that involve layering hair to make it appear thicker include point cutting, feathering, and long layers. Adding volume and texture to the hair can be achieved by cutting the hair at an angle, which is known as point cutting. It involves texturing the hair by softening blunt ends and cutting them at an angle, thus helping to create the appearance of fullness and volume in the hair. In addition to texturing, one can achieve a hairstyle with movement and volume by feathering. Feathering is a technique that aims to shape and blend the tips of the hair to reduce bulk in targeted areas while enabling free-flowing movement. Of all the methods, long layers offer the most benefits when it comes to maintaining the length of the hair while layering patterns are added, which can help increase the perceived volume of the hair. These techniques enhance their effectiveness with styling tools or thickening products.
Which layered styles work best for women with thinning hair?
Soft, wispy layers are the best choice for women with thinning hair because they add movement without removing too much weight. Face-framing layers also work well by shifting focus from denser sections of the hair to areas with low density and enhancing one’s overall appearance. Textured bobs and layered lobs are shoulder-length or slightly shorter cuts that create a structured shape while also adding the illusion of extra volume. The hair can keep its body without looking flat or heavy by using light feathering at the ends. Work with a stylist specializing in layered styles to achieve the optimal look and ensure the best results.
How do layers add volume to fine hair?
Fine hair can benefit from voluminous layers to create more movement and liveliness. Having poor volumization will lead to flat or lifeless hair. Layers are expertly cut at various lengths to alleviate weight while retaining lift at the roots and through the strands. Adding height and fullness to the crown is achieved from shorter layers with added texture and bounce through staggered lengths, giving way to lively curls. This approach will break any monotony in the hair while adding more texture and vitality, offering fine hair a much more voluminous appearance. Strategic layering allows for better distribution of styling and volumizing sprays, amplifying the overall effect.
What are the best medium-length layered hairstyles for women over 60?
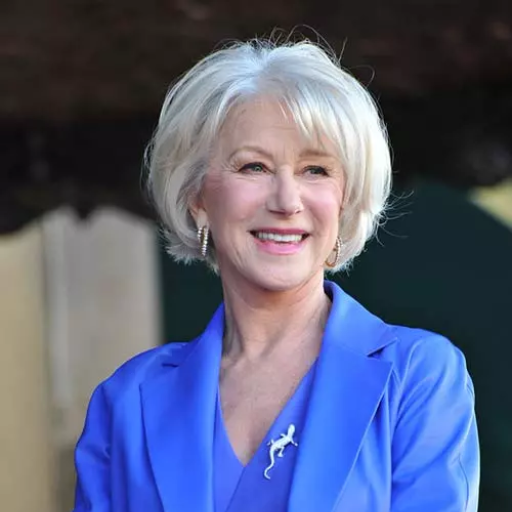
When choosing the most suitable medium-length layered hairstyles for women over 60, it is vital to focus on styles that accentuate facial features, add volume, and are easy to care for. The classic layered bob is a versatile choice as it beautifully contours the face while providing fullness. Likewise, a feathered cut with soft layers helps bend the rules regarding age by capturing movement and a youthful appearance for those wanting more dimension; shoulder-length shag cuts with wispy layers and side-swept bangs provide a contemporary look for thinning hair. These styles are easy to maintain and flattering, highlighting how adaptable the reductions are to different hair textures, styles, and personal preferences.
How can a layered lob flatter older women?
Older women can benefit from a layered lob, which draws attention to the beauty of facial structure while creating a youthful aura. This newer look has all the benefits of volume and texture without the effort of thinning hair or fine strands. The length’s versatility also allows for softer waves, straight finishes, or subtle curls, giving many styling options. A layered lob also captures attention and softly frames the face with an elegant look suitable for older women’s varied needs while needing little effort to maintain.
What are the benefits of a medium-length layered cut?
Medium-length layered cuts have several advantages. They add volume and texture, boosting the overall look of fine or thinning hair. The layers also enable styling flexibility; I can effortlessly transform from a sleek, straight look to soft, natural waves. Moreover, this cut highlights my features and flatters different face shapes while requiring low maintenance to keep it fresh and modern. It’s a practical yet stylish hairstyle that enhances my youthful appearance.
How do you style a medium-length layered haircut for different occasions?
Depending on the occasion and the preferred hairstyle, a medium-length layered haircut may be styled differently. For casual outings, beachy waves are another versatile option, easily styled with a curling wand and texturizing spray to flaunt the hair’s natural layers. For work and other formal occasions, the hair can be flat ironed and polished with smoothing serum for a sleek look that highlights the sharpness of the layers. Soft curls and half of the hair pinned up create a polished yet romantic style ideal for most special occasions, often finished with tiny accessories such as clips and pins. Since layers add versatility, they can be styled according to one’s mood and the occasion.
Which layered hairstyles work well with gray or grey hair?
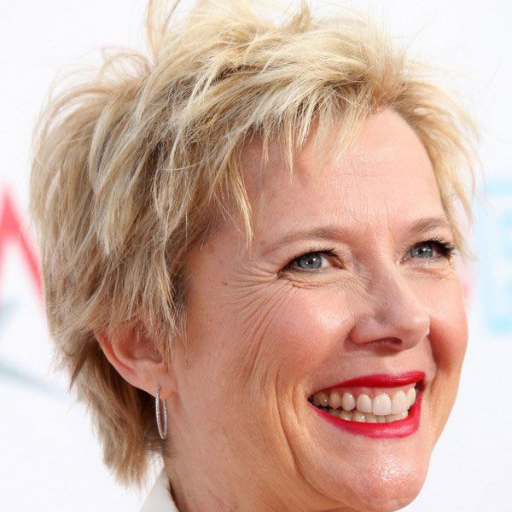
Layered hairstyles add movement and dimension to gray hair, ensuring it does not appear flat. The shoulder-length layered cut is perfect because it is graceful yet practical and allows texture to do the work. A layered pixie cut is soft and voluminous for shorter hair while still contemporary and sharp. Long, cascading layers infused with gentle waves or curls emphasize the contrasting tones within gray hair, creating an elegantly flowing look. These styles showcase beautifully natural grays and versatility for any occasion.
How do layers enhance the appearance of grey hair?
Layers are essential to gray hair because they add movement and dimension, making it look fuller and easier to style. They also add texture, making the gray hair look less dull, especially since it may lose some of its shine. With layering, the different shades of gray, such as silver, white, and darker streaks, can be enhanced as the hair catches light in various ways, showcasing the beauty and vibrancy of the hair. In addition, using layers can enhance other features as they help soften them, creating a youthful and polished appearance. This makes layered styles perfect for displaying the graceful beauty of gray hair.
What are some stylish layered cuts for women embracing their gray?
An example might be a long layered style with soft waves, which maintains length while increasing movement and texture. For people who prefer shorter styles, a pixie cut offers a modern, easier-to-manage style that draws attention to the varying shades of gray. Shoulder-length layered bobs are another versatile option, as they beautifully frame the face and can be styled straight or wavy.
How do you maintain layered gray hairstyles?
Layered gray hairstyles require care and proper attention like any other stylized hair. For maintenance, start with an effective shampoo and conditioner targeted explicitly to gray or silver hair; ensure it is sulfate-free to preserve the luster and avoid the brassy tone. Also, add a deep-conditioning treatment every week to restore moisture since dry gray hair is often firmer than black or brown hair. Additionally, consistent trims every 6-8 weeks go a long way in maintaining the shape of the layers while avoiding split ends. Use styling products like lightweight mousses, texturizing sprays, or serums to boost volume and layer definition. Lastly, heat-styling tools should be paired with regular hats or UV-protectant sprays to safeguard delicate strands from harsh sun damage.
What are some trendy layered haircuts for women over 60?
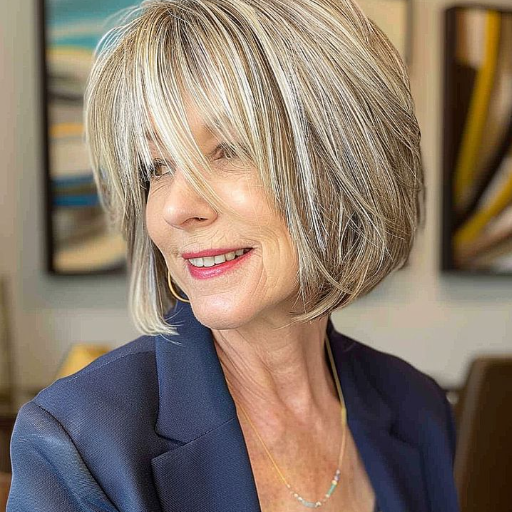
Some modern, feminine haircuts for women above 60 years include the layered classic bob with a contemporary feel and polished finish. Another one is layered pixie cuts, which are ideal for adding dimension and texture to finer strands. For women preferring to keep their hair long, soft waves with gentle layering cascading down their backs can be styled to look youthful and sophisticated. Women with active lifestyles and those not looking for something high maintenance would enjoy the shag cut with feathery layers as it creates volume and movement effortlessly. Adding sidelong or wispy bangs helps soften the look while drawing attention to the cheekbones and along the edge of the jaw.
How can curtain bangs complement layered hairstyles?
Layered cuts can be significantly enhanced with bangs. However, curtain bangs truly take the style to a different level as they integrate smoothly into the fringe and enhance the layering, thus creating a flow that cannot be compared. The softest elements of framing work to soften the face shape while drawing attention to features, creating an accent for loose curves. In addition, curtain bangs are easily blended with layered bang styles, adding effortless volume and texture. Styled casually or dressed, they can still suit formally while effortlessly adapting to layers.
What are some edgy layered options for older women?
For older women who want to incorporate an edgy element into their hairstyles, some bold shag hairstyles and layered styles stand out. A shag haircut with tousled layers has an effortless, youthful aura along with added volume and texture. Complementing it with asymmetrical curtain bangs can add striking boldness and accentuate features. A layered bob with sharp, angled ends can add a sleek and modern appeal that goes well with gray or silver tones. More daring options include long layers with an undercut or shaved trim tailored to unique personalities and preferences. These styles offer versatile, bold looks while requiring minimal maintenance.
How do you incorporate side-swept bangs into layered cuts?
To integrate side-swept bangs into layered cuts, I think first about the length and density of the hair so that the bangs connect to the layers without harsh lines. My preferred method is to cut the bangs at an angle and blend them into the driving layers so that they merge without harsh lines. To achieve the desired outcome, the bangs can be textured using a razor or point-cutting technique, depending on the desired result. This method is especially effective for long-layered cuts and bobs where dimension, ease of styling, and versatility are desired.
How do layered hairstyles work for different hair textures?
Layered haircuts are versatile in that they can enhance several hair textures by lifting and showcasing their unique qualities. Straight hair has movement added, and the flattery shape is avoided by adding gentle volume and subtle layering at the ends of the hair. Layers that differentiate and emphasize the hair’s natural waves provide a soft, effortless appearance. About curly hair, volume control is achieved through strategic layering, which reduces bulk and defines curls instead of simply placing them in a pyramid shape. Thick or coarse textures are controlled using strategically placed layers to remove excess weight and improve manageability. In contrast, finer textures appear fuller due to clever layering that creates an illusion of volume. This strategic approach to layering based on the different textures allows for balance, beauty, and practicality.
What are the best-layered cuts for curly hair?
Each cut strives to give shape, remove bulk, and let the curls fall naturally. The curly shag cut is very popular because it has shorter layers on top and is tapered for ease of movement. The shoulder-length layered cut also frames the face but helps maintain the structure and control bulk. The rounded, layered cut also gives a bold style by creating a halo that accentuates the definition of the curls and creates a soft, stylish shape. These cuts focus on the health and structure of curls, ensuring ease of management and a pleasing look.
How do you style layers in straight or fine hair?
The techniques for styling straight or fine hair layers involve working with the hair’s volume, texture, and movement. It begins with the application of volumizing mousse or volumizing spray. The roots need to be lifted. Blow-dry using a round brush. Add soft curves and shapes to the layered sections. To achieve more texture, a flat iron or curling wand can curl or slightly wave the ends of the layers. This also gives the hair more thickness and dimension. Finish with hairspray, but ensure it is light-hold; this will maintain the shape while the hair is not being weighed down. Reliance on hair products that enhance volume and texture is essential for achieving the best results for regular trims.
Which layered hairstyles suit wavy hair textures?
Wavy hair looks best with a layered cut accentuating its movement and texture. Long layered cuts are ideal because they reduce volume while accentuating the waves. This will make hair look soft and light. Medium to long voluminous cuts are also a great choice because they provide texture while keeping it voluminous for an effortless style. Curtain bangs with face-framing layers can soften and add a beautiful definition for an edgy yet modern hairstyle. When styling your hair, using a light-hold curl-enhancing product is always best to accentuate the natural waves without making your hair look stiff.
Frequently Asked Questions (FAQ)
Q: What are some of the best medium-length hairstyles for women over 60?
A: Some of the best medium-length hairstyles for women over 60 include the long bob, layered cuts that frame the face, and soft, textured styles. These haircuts are perfect for creating the illusion of fuller hair and are easy to style. They can be customized to suit different face shapes and hair textures, making them versatile options for many older women.
Q: How can a side part enhance hairstyles for women over 60?
A: A side part can be a great addition to hairstyles for women over 60, adding volume and dimension to the hair. It can help frame the face beautifully and create a more youthful appearance. Side parts work well with medium-length hairstyles and can be incorporated into various styles, from straight hair to curly bobs.
Q: What are some flattering hairstyles for women over 60 with fine hair?
A: For women with fine hair over 60, flattering hairstyles include layered cuts that add volume, textured bobs, and pixie cuts. These styles can make hair appear fuller and thicker. Incorporating layers around the face and throughout the rest of your hair can create movement and the illusion of more volume. Low-maintenance options like a short, layered pixie cut can also be great for fine hair.
Q: Are there any medium-length hairstyles that are particularly easy to style for women over 60?
A: Yes, several medium-length hairstyles are easy to style for women over 60. A long bob with subtle layers is low maintenance and versatile. Soft, wavy styles that frame the face are also simple to achieve with the right hair products. These hairstyles and haircuts for women can be styled quickly and still look polished.
Q: How can layered hairstyles benefit women over 60?
A: Layered hairstyles can significantly benefit women over 60 by adding volume, texture, and movement to the hair. They can help disguise thinning hair or hair loss, which is common in older women. Layers around the face can soften features and create a more youthful appearance. Layered cuts are often easier to style and maintain than one-length haircuts.
Q: What popular haircuts for women over 50 that work well into their 60s?
A: Popular haircuts for women over 50 that work well into their 60s include the classic bob, layered shoulder-length, and sophisticated pixie cuts. These timeless styles can be adapted to suit changing hair textures and face shapes. Medium-length hairstyles for women in this age group are exceptionally versatile, balancing ease of styling and the ability to create various looks.
Q: How important is hair color in choosing the best hairstyles for women over 60?
A: Hair color is crucial in choosing the best hairstyles for women over 60. The right hair color can complement your skin tone, brighten your complexion, and enhance the overall effect of your hairstyle. Many women in their sixties opt for softer, more natural-looking colors or embrace their gray hair. The choice of color can also impact how your haircut looks, potentially making it appear fuller or more textured.