Across numerous industries, PVC tarpaulins are well known for their versatility and durability. Finding a dependable supplier becomes imperative whether you need heavy-duty covers, waterproof linings, or other custom fittings. This blog post offers a detailed overview of the leading PVC tarpaulin wholesalers and suppliers around the globe, including those with competitive prices for wholesale purchases. We will examine their product catalogs, distinguishing characteristics, and considerations for the appropriate supplier. After reading this article, you will know the best suppliers for your PVC tarp needs.
What Makes a Reliable Plastic Tarpaulin Manufacturer?
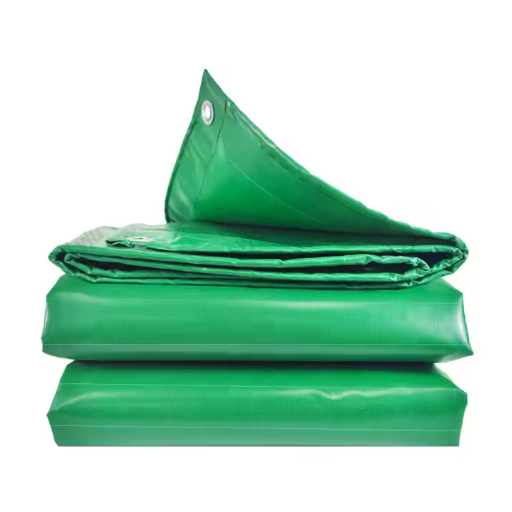
Good manufacturers of plastic tarpaulin products should offer high-grade and sturdy materials resistant to different climates. Seek those who guarantee consistent quality through certifications and other assurances. Other reliability indicators include value for money, quick turnaround times for product delivery, and good after-sales support. For these reasons, look for manufacturers with comprehensive catalogs, flexible customization options, and effective client relations to meet all your business expectations.
Key Quality Standards for PVC Tarpaulin Manufacturers
It is essential to look at the specific quality benchmarks to guide you on the effectiveness, durability, and reliability of a PVC tarpaulin to ensure that set functionalities are met when looking at different manufacturers. One of the key considerations is that they need to have international quality management ISO 9001 certification and REACH compliance, which also ensures that the materials used are safe for the environment. Employing the relevant raw materials, such as premium PVC-coated fabrics, guarantees abrasion resistance, waterproofing, and UV protection.
Furthermore, the evaluation should include the performance of quality checks throughout the entire process, like assessing the tensile strength and checking for fire retarding. For every manufacturer, a range of set application needs that can be tailored should also be provided, backed by advanced machinery and technology that enable precision. A transparent warranty and service manual and documented processes are critical and depict the effort put towards quality and satisfaction post-sales while also covering their after-sales commitments.
How to Evaluate a Tarpaulin Factory’s Production Capabilities
Assessing the capacity of a tarpaulin factory requires checking for particular steps to meet the operational quality set by the industry norms. Check the company’s certification; if they have ISO, they follow international quality management practices. Also, check the types of raw materials they have in stock; high-grade materials such as polyethylene or PVC polymers greatly enhance the end product’s durability and performance. Check the production potential by asking about the type of machines they have, the degree of automation, and their daily output, all of which show efficiency and scalability.
Next, check the quality control procedures. Thorough testing is needed for waterproofing, UV resistance, and tensile strength. Think about going to the factory to ensure all the safety and environmental regulations are followed. Also, check the degree of customization offered; of interest will be unlimited flexible sizes, colors, and additional reinforcements or eyelets.
Lastly, look up what previous customers say and any case studies available to understand their performance records. Good factories provide transparent production documents and reliable after-sales support, such as timely warranties and replacements within stipulated timelines. These factors allow you to find a factory with well-developed production and quality control systems.
Importance of Supplier Certifications and Quality Control
Supplier certifications and quality control are critical in maintaining product standards and uniform reliability. ISO 9001 is an example of a certification that shows a supplier practitioner one of the international quality standards for verifiable systems of managing processes. This guarantees their m apprehensible processes are efficient and capable of yielding high-caliber products. Industry-specific certifications can also attest to compliance with some set regulations and safety.
In terms of the integrity of the product, maintaining that form is also achieved through control quality processes. Regular inspections and monitoring at different production levels greatly assist in timely defect detection, minimizing the chances of expensive errors or delays. Strong control systems and industry-recognized certifications strengthen trust and reduce risks while ensuring products are up to standard, compliant, and consistently supplied as expected. Emphasizing such suppliers amply protects the supply chain while sustaining customer expectations and satisfaction.
How can you source wholesale PVC tarpaulins at factory prices?
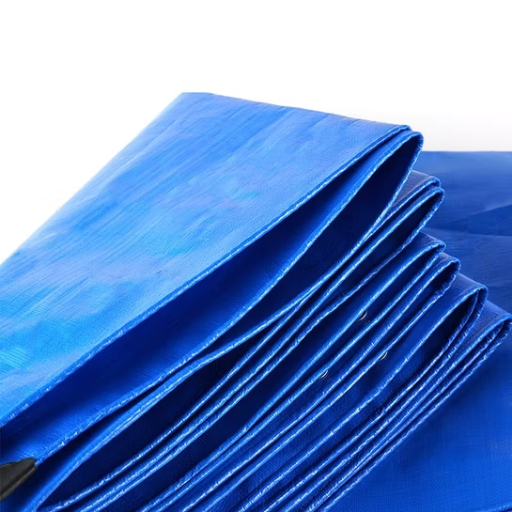
Research reputable manufacturers instead of dealing with middlemen to obtain wholesale PVC tarpaulins at factory prices. Check out Alibaba and Global Sources or attend trade fairs for specific industries to find suppliers with good reputations and sell at competitive prices. Verify their credentials, production capacity, and quality control systems to ascertain their reliability. Negotiating favorable terms for bulk orders and establishing long-term relationships will guarantee the best factory prices. Finally, check multiple quotations and request samples to verify the quality before purchasing.
Benefits of Buying Tarpaulin Rolls Directly from Manufacturers
Buying tarpaulin rolls from the manufacturers directly comes with numerous benefits. First, it usually comes with considerable savings, especially in bulk purchases, as you’re not paying for intermediaries, and the direct price offered is more competitive. They will also provide customization to specify the required sizes, materials, and colors. Also, dealing with manufacturers directly ensures a constant supply of high-quality products since they have stringent quality control measures put in place. They are also easy to talk to, offering quick replies to questions or requests referring to reorders, making the procurement process smoother. Without third-party distributors, better transparency and long-term partnerships for your purchasing needs are built.
Factory Wholesale Pricing: What to Expect and How to Negotiate
Unlike retail pricing, factory wholesale pricing can result in significantly lower costs because you are cutting out middlemen. Manufacturers tend to work with large volume sales, so minimum order quantities (MOQs) might apply. Quality consistency and punctuality are significant factors in wholesale transactions. Moreover, payment terms may include upfront deposits, staggered payments, or periodic payments during certain stages of the agreement.
To negotiate successfully, begin with understanding preferred market prices and familiarizing yourself with the typical cost of the desired products. Cultivating good relationships with manufacturers will help place trust and foster favorable terms. Emphasize your capacity to be a long-term client for better pricing or flexibility on MOQs. Use data and competitor comparisons to showcase the value you offer through order volume or partnership, and don’t hesitate to ask for discounts. Maintain open communication with the manufacturer and be willing to make reasonable concessions, and you are likely to reach a more favorable outcome. Clear communication and the willingness to make sensible compromises lead to successful negotiations.
Minimum Order Quantities and Bulk Purchasing Guidelines
Manufacturers usually impose a limit on Minimum Order Quantities (MOQs) for cost and production purposes. These demands help a business function by minimizing waste, maximizing resource allocation, and improving workflows. The proposal can be made by showing the business’s potential, considering realistic changes, or proposing alternate agreements such as tiered pricing.
When ordering in bulk, remember to focus on economies of scale, which in turn lower costs per unit. Suppliers should be worked with to gain additional benefits such as more discounts, longer payment periods, or a higher level of customization. Consistently monitoring consumer demand and inventory levels helps prevent overstocking or excess capital investment issues. Price offered by industry competitors should also be considered to keep negotiations balanced.
Maintaining constant communication with dependable suppliers ensures agreement on order quantities, shipment dates, and timelines. Adapting to find common ground where the supplier’s needs and business goals clash positions oneself to form advantageous relationships.
What Customization Options Can Plastic Tarpaulin Manufacturers Provide?
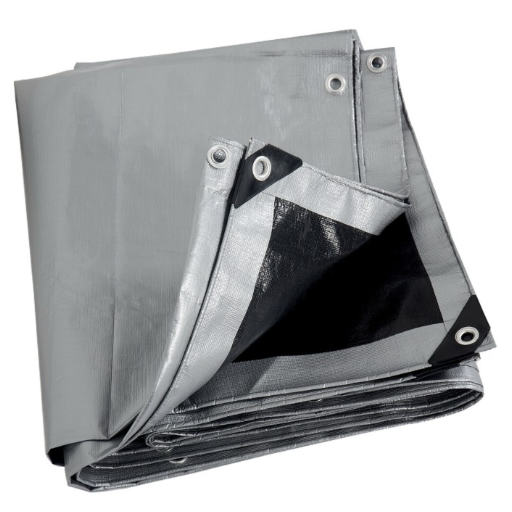
Manufacturers of plastic tarpaulin can offer a variety of customizations to particular industry needs. These options include differences in height and width, depth, and the hue of the tarp. Customizations could also be facilitated for the material used in construction, such as coatings classified as UV resistant, flame retardant, or waterproof, which add to the strength and purpose of the product. Other customizations aided by logo grommets and printed tape edges could add to the brand recognition and customers’ perception. With these options, the manufacturers can be sure that they will meet the customers’ exact needs.
Custom PVC Tarpaulin Colors, Sizes, and Specifications
PVC tarpaulins are the most versatile offer due to the customizations they offer. Tarpaulins are provided to the market in many colors, including but not limited to blue, green, white, black, and transparent, depending on the application for industrial, marketing, and outdoor purposes. Customization is available in color and size, which makes it possible to design the custom size required, from small sheets to large covers for larger projects. It’s broken down into two ranges. The first is classed as standard, with a variety of 0.35mm to 2.0mm with moderate strength and flexibility, and the second customizable option is thickness.
As for other features, such as flame-resistant treatments, UV protection, mildew resistance, and waterproof finishes, manufacturers allow customization to add unique features for specific projects. Additional heavy-duty grommets, reinforced edges, and optional logo printing enhance branding possibilities & functionality. Such customization guarantees meeting the demands of agriculture, construction, and logistics industries with PVC Tarpaulin.
Specialized Treatments for Waterproof PVC Coated Tarpaulins
Waterproof PVC-coated tarpaulins undergo various specialized treatments to maximize their durability and performance for multiple applications. Adding: anti-slip surface coatings to enhance safety, complete water penetration guarantees, and mildew resistance to safeguard against fungi in humid conditions. Other options include thermal insulation layers for temperature control and anti-static treatments for specific industrial requirements. Adding grommets, complete grommet holes, waterproof finishes, UV stabilization, and flame-resistant coatings, PVC tarpaulins prove their versatility and reliability and endure demanding environments across various industries.
Branding and Printing Options for Wholesale Tarpaulin Orders
Most wholesale tarpaulin orders have customizable branding and printing options to suit individual business requirements. A company can promote its products or services by printing logos, taglines, or promotional messages on the tarps using standard methods like screen or digital printing and heat transfers. These advanced printing techniques ensure that the graphics are bold, vivid, long-lasting, and will not wear out or fade even when exposed to harsh outdoor conditions. Furthermore, some manufacturers provide design templates that help boost brand recognition by offering full-color printing and custom designs. Usually, businesses ordering in bulk have various choices about the size, color, and finish of the tarpaulins, so these will align with the firm’s corporate branding requirements and marketing objectives.
What Technical Specifications Matter When Ordering Plastic Tarpaulins?
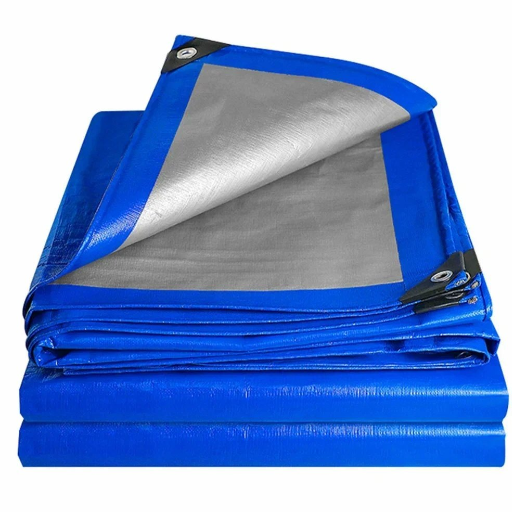
When ordering plastic tarpaulins, some underlying factors must be addressed to accomplish the goals. These factors include choosing the right plastic materials and their associated properties. The first focal point would be the thickness of the material that will be measured in mil or GSM (grams per square meter). This will indicate how long the tarp will be considered durable. UV protection is necessary whenever the tarps are used outdoors for long periods as this will inhibit thwarting caused by sunlight. In addition to these factors, the capacity to be waterproofed must also be evaluated in terms of patrol from rainwater and moisture. Borders without limbs, together with grommets that make the tarpaulins stronger and easier to install, will enhance the performance of the tarp. Also, size, color, and printing options should serve the intended application or branding regardless of custom tailoring such options.
Understanding GSM Ratings in PVC-Coated Fabric Tarpaulins
The term GSM, or grams per square meter, describes a metric that defines the weight of the fabric while fundamentally indicating its quality and how long it will last. Generally, stronger tarpaulins used for heavy-duty industrial covers or transportation tend to have higher GSM as they are thicker and more hard-wearing. On the other hand, lower GSM fabrics are more straightforward to bend and lighter, making them suitable for more temporary uses.
Knowing the required GSM while selecting a PVC-coated fabric tarpaulin is crucial to ensuring the end product aligns perfectly with your requirements. For more lightweight tasks, fabrics between 200 and 400 GSM will do, while 500-700 GSM is more suited for medium-duty workloads. Extreme durability tarpaulins with 800 or above GSM are ideal for harsh industrial or construction purposes.
Make sure the fabric with higher GSM ratings aligns with your application’s environmental conditions and demands since they are generally weather resistant, UV protected, and tend to last longer.
Waterproof PVC Tarpaulin Standards and Testing Methods
The performance of waterproof PVC tarpaulins in varying applications is ensured via rigorous standards and comprehensive testing. Water resistance, tensile strength, tear resistance, UV resistance, and flexibility are some of these tarpaulins’ fundamental parameters of interest. Measurement standards like ISO 2286-2 and DIN EN 1876 are placed to evaluate weight, thickness, and coating adhesion to guarantee maintenance of manufacturing quality.
Testing techniques generally include subjecting the tarp to high water pressure to test impermeability, while other evaluating methods include using tensile and tear strength machines to test physical durability. Testing of UV protection consists of exposing the tarp to prolonged exposure to artificial solar radiation to estimate its long-term resistance to deterioration. In addition, some flexibility tests are performed at extremely low temperatures to increase the tarp’s reliability in variable weather conditions. These standardized procedures allow manufacturers to ensure that industrial and commercial standards are met for PVC tarpaulins.
Custom Specifications for Truck Cover and Awning Applications
While selecting PVC tarpaulins for covers and awnings for trucks, issues such as flexibility, durability, weather resistance, and overall strength are essential. The material must have a high tensile strength to bear heavy usage and resist tearing during transport or outdoor exposure. To safeguard against the damaging effects of sunlight, UV stabilization is essential for halting color fading and degrading the material’s integrity. In addition, waterproofing guarantees protection from rain and leakage, which is critical for cargo safety. For awning applications, the fabric must possess a certain amount of elasticity to maintain tension and shape while being lightweight for ease of installation. Long-term functionality anti-mildew and flame-retardant features must also be integrated to comply with safety standards. Considering all these factors will ensure PVC tarpaulins can withstand the rigors of use for both transportation and shading purposes.
How Do China Manufacturers Compare to Other Tarpaulin Suppliers?
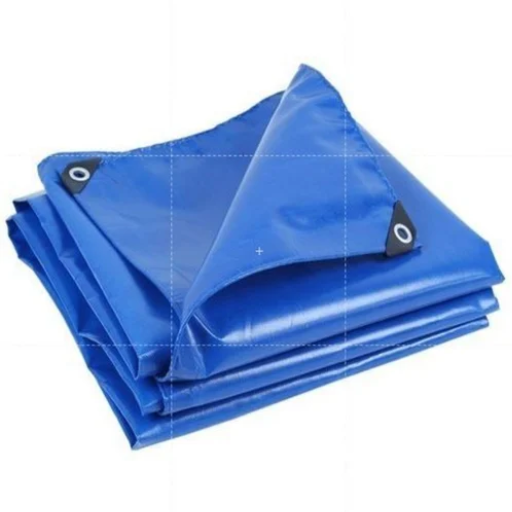
China manufacturers are often distinguished by their cost-effective production methods, offering competitive pricing without sacrificing quality. Many of these manufacturers have invested in advanced machinery and technology for producing durable tarpaulins. Furthermore, Chinese suppliers grant an extensive range of customization options, from material selection to branding, which cater to various market needs. Still, it’s prudent to conduct comprehensive research regarding the supplier’s international quality certifications and after-sales support reliability to ascertain the value of choosing these low-cost products.
Advantages of Working with Leading PVC Tarpaulin Factories in China
Cost-Effective Production: China’s leading PVC Tarpaulin factories offer competitive pricing because of advanced manufacturing processes and economies of scale. This enables businesses to acquire high-quality tarpaulins at cheaper prices than other suppliers.
Customization and Versatility: Many top-tier factories also offer a high degree of customization, including different thicknesses, colors, sizes, and finishes. Such flexibility enables businesses to customize products for industrial covers or outdoor utility.
High-Quality Standards: The best factories have stringent quality control processes for products certified for at least ISO certification. This certifies the product for durability, UV resistance, and waterproofing for long-term usage.
Efficient Logistics and Global Reach: These factories are situated in major industrial zones and enjoy developed supply chains and shipping networks. This guarantees timely delivery to global markets, reduces downtime, and maximizes operational efficiency.
Robust After-Sales Support: Top manufacturers emphasize building lasting relationships with their customers by providing reliable after-sales support, which includes technical support, warranty terms, problem-solving, and improving overall customer satisfaction.
Quality Control Processes of Top Tarpaulin Suppliers
Leading tarpaulin suppliers have enabled comprehensive quality control systems to ensure their products meet standards. The included procedures are:
Material Inspection: The raw materials undergo inspection for polyethylene or PVC to check their strength, durability, and chemical composition. This enables the verification of the base materials necessary for creating high-quality tarpaulin.
Production Monitoring: Using advanced machinery with standardized procedures makes defect prevention possible. Product quality at all levels is monitored and controlled throughout each process of lamination, coating, and weaving.
Strength and Durability Testing: The finishing processes of the tarpaulin involve testing for tensile strength, waterproofing capabilities, UV resistance, and tear resistance, all of which simulate severe, reliable environmental conditions.
Compliance with Standards: Reputable suppliers also ensure that their tarpaulins meet international quality standards and have an ISO certification. That way, they can prove they provide safe, reliable products.
Customer Feedback Integration: Top suppliers are known to include customer feedback in their processes, which helps adjust necessary changes where product performance did not change the expectations that were set.
Comprehensive quality control at all levels ensures the utmost dependability of products for multiple uses, making us the best tarpaulin suppliers.
Comparing Polyester Fabric Tarpaulin Options Globally
When analyzing leading sources from across the globe, a specific pattern emerges regarding the options available for tarpaulin made from polyester fabric. Their widespread use comes from their low weight, remarkable durability, and resistance to water, UV rays, and tearing. Furthermore, they are often coated with PVC or polyethylene, increasing their utility in agriculture, construction, and transportation.
Suppliers worldwide vary significantly in terms of pricing, customization, and the quality of goods manufactured. European manufacturers are known to provide products of premium quality that use innovative coatings to ensure long-term durability in harsh climates. In contrast, Asian suppliers, especially those from China or India, offer budget-friendly options and bulk production flexibility tailored to large-scale businesses. Lastly, North American producers focus on the environmental standards of their products by using eco-friendly coatings and recyclable materials.
Factors like budget, tensile strength of polyester tarpaulin, and weather resistance influence the choice of appropriate tarp. Businesses can analyze various global suppliers to achieve the most favorable price while balancing other demands like quality and sustainability. Always look at warranty, certification, product reviews, and other factors to help make an informed decision.
References
Frequently Asked Questions (FAQ)
Q: What are the differences between PVC tarpaulin and PE tarpaulin?
A: PVC tarpaulin is made from polyvinyl chloride material and is typically more durable and heavier than PE tarpaulin. PVC tarps offer superior tear resistance, UV protection, and waterproof capabilities, making them ideal for long-term outdoor applications. PE tarpaulin (polyethylene) is lighter, more affordable, and still offers decent water resistance for temporary coverage. While PVC tarpaulin material has greater tensile strength and flexibility, PE tarpaulin is more common for light-duty applications and temporary covers. PVC tarps are also better suited for extreme weather conditions.
Q: How do I choose the right PVC tarp for my needs?
A: When selecting a PVC tarp, consider the intended use, required durability, and environmental conditions. Choose a thicker material for heavy-duty applications like truck tarpaulin or industrial covers (at least 600-900 gsm). Check the quality of PVC coating and ensure proper reinforcement at seams and grommets. For permanent outdoor installations, select UV-resistant, high-quality PVC tarps. Consider whether you need a waterproof, heavy-duty option or a lighter cover tarpaulin. Reputable PVC tarpaulin manufacturer factories can guide specific requirements and often offer customization. While price matters, investing in better quality typically provides a longer service life.
Q: What are the advantages of HDPE tarpaulin over other types?
A: HDPE tarpaulin (High-Density Polyethylene) offers several distinct advantages. It’s significantly lighter than PVC tarpaulin while maintaining excellent tensile strength. HDPE tarps provide superior UV resistance and are ideal for prolonged sun exposure. They’re also more environmentally friendly than PVC options as they’re recyclable. HDPE tarpaulin is breathable, which helps prevent condensation and mildew buildup. While not as waterproof as PVC fabric, HDPE tarps offer good water resistance. They’re particularly popular for agricultural applications, construction site coverage, and situations where weight considerations are essential.
Q: How are vinyl tarps different from canvas tarpaulin?
A: Vinyl tarps (PVC tarps) and canvas tarpaulin differ significantly in material and performance. Vinyl tarps are made from PVC-coated polyester fabric, offering excellent waterproofing, UV resistance, and durability in harsh weather. They’re typically more affordable and require less maintenance. Canvas tarpaulin, traditionally made from cotton or linen (sometimes with PVC laminated tarpaulin technology), provides better breathability and a classic aesthetic. Canvas is typically heavier, expensive, and requires more maintenance to prevent mildew, but many users prefer its natural look and feel. Vinyl tarps are usually the better choice for industrial applications requiring waterproof properties, while canvas may be selected for aesthetic applications.
Q: What should I look for when purchasing PVC tarpaulin fabric by the roll?
A: When purchasing PVC fabric roll or PVC tarpaulin roll, first verify the material thickness (measured in gsm – grams per square meter) based on your application needs. Check the reinforcement type to see whether it’s mesh-reinforced for added strength. Confirm UV protection capabilities if for outdoor use. Examine the fire-retardant properties if relevant to your application. Verify the roll dimensions and ensure they match your project requirements. Quality control is crucial – reputable suppliers like those from China tarpaulin manufacturers or specialized LTD companies should provide testing certifications. Finally, compare prices across different suppliers, but remember that extremely low prices often indicate substandard materials that won’t deliver the performance or longevity you need.
Q: How do waterproof tarpaulin covers perform in extreme weather?
A: Waterproof tarpaulin covers, incredibly heavy-duty waterproof varieties made from quality PVC, perform exceptionally well in extreme weather. Premium truck cover tarpaulin and tarpaulin awning products can withstand heavy rainfall, strong winds, and snow loads when adequately secured. The best waterproof tarps feature reinforced edges, strong grommets, and heat-sealed seams to prevent water penetration. In high temperatures, high-quality PVC tarpaulin for tent applications resists UV degradation and maintains flexibility. However, even the best tarps require proper installation with adequate tension and secure fastening. Look for products labeled as heavy-duty with proper thickness (700-900 gsm) from established manufacturers for extreme conditions.
Q: Where can I find wholesale PVC tarpaulin suppliers with the best prices?
A: The best wholesale PVC tarpaulin suppliers are typically found in Asian manufacturing hubs, particularly from China PVC tarpaulin producers. Many established factories offer direct purchasing options through alibaba.com, made-in-china.com, and similar platforms. For reliable quality, look for suppliers with ISO certifications and those willing to provide material samples. Established PVC tarpaulin manufacturer factories in China, Vietnam, and India typically offer the most competitive pricing on bulk orders. Consider minimum order quantities, shipping costs, and payment terms when comparing quotes. European and North American distributors often source from these Asian manufacturers but may offer quicker delivery for smaller orders, albeit at higher prices.
Q: What makes coated PVC tarpaulin better than standard options?
A: Coated PVC tarpaulin offers superior performance characteristics compared to standard options. The PVC coating process protects against water, UV rays, and physical damage. This additional protection makes the tarpaulin sheet significantly more durable and longer-lasting. Premium-coated PVC tarpaulin features enhanced tear resistance and often includes anti-fungal and flame-retardant properties. The coating also improves flexibility and ease of handling in various weather conditions. While standard tarps might suffice for temporary applications, coated options, such as truck tarpaulin, industrial covers, and outdoor storage, are essential for longevity applications. The specialized coating technology used by quality manufacturers results in a product that maintains its protective properties much longer than basic alternatives.