Material testing is crucial in various industries, as materials must possess a certain level of strength and durability. Among the many tests, bending is one of the most basic methods for testing a material’s ability to resist deformation under stress. To maintain quality and safety in your project, whether in manufacturing, construction, or product development, it is essential to understand bend test machines and their capabilities thoroughly. The article examines the operation of bend test machines, including their components and the information obtained from these testing machines. By the time you finish reading, you will fully understand why this testing method is essential and how it ensures material performance under more demanding applications.Click here to read more
Introduction to Bend Test Machines
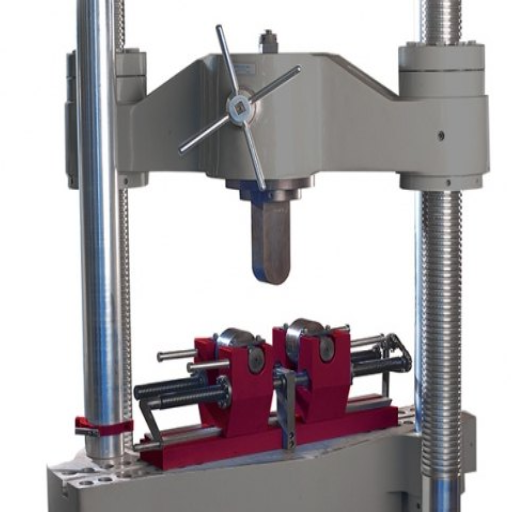
What is a Bend Test Machine?
The bend test machine is a specialized tool used to determine the ductility, strength, and resistance of materials to bending forces. Testing of this kind is conducted in the construction, aerospace, and manufacturing industries, among others, to ensure that materials meet specific standards of performance. This machine applies a bending force with precise control, and consequently, measures the material’s ability to undergo deformation without cracking, brittling, or outright failure. Its ability to test the flexibility of a material and its structural dependability becomes useful in applications involving mechanical stress.
Such machines would typically incorporate key components, including a loading mechanism, material-holding fixtures, and precision measurement devices, to evaluate the amount of bending and its effects. Depending on the nature of the tests to be performed, the load may be adjustable in terms of force, bend angle, and specimen dimensions, thus offering an extensive range of tests for materials such as metals, plastics, and composites. This test data ensures that materials are tested according to industrial standards and material design optimizations to minimize structural failures under actual conditions.
Present-day bend test machines are equipped with various advanced features, including automation, real-time data analysis, and comprehensive reporting, thanks to modern innovations. Such features enhance the efficiency and accuracy of testing procedures, improve repeatability, and reduce human intervention. For the expert who works in quality assurance or downtime reduction of materials during testing and improving the safety factor of a product, bend test machines find their crucial place in the material testing arena.
Importance of Bend Testing in Material Science
Industrially, bend testing is used to determine the mechanical properties of materials and ensure their integrity. A bend test assesses flexibility, strength, resistance to deformation under stress, and so on. The yield point, flexural strength, and modulus of elasticity measurements help in determining the suitability of their application in various industrial settings. Such applications are critical in construction, aerospace, and automotive fields, where loads placed upon materials become crucial to the safety and efficiency of a product. The data obtained from bending tests is precise enough to warrant the storage, unambiguity, quality, and safety of infrastructure materials or machinery.
Modern advances in bend testing have further enhanced the very nature of bend testing and its implications in materials science. The latest systems, equipped with sensors and AI software, provide highly detailed, real-time results that can be acted upon quickly during development and production. These systems are capable of testing traditional materials, such as metals and plastics; however, they are also increasingly crucial for testing advanced composites and nanomaterials. For example, composites used in aerospace engineering require extensive bend testing to ensure that they can withstand extremely harsh conditions while remaining lightweight. Being able to rely confidently on accurate bend test data will undoubtedly accelerate the pace of introducing new materials by these industries, and hence their product design and functional direction.
Bend Test Applications Overview
Bending tests are used in numerous industries to measure material performance under stress, ensuring the material’s durability and reliability in critical applications. Bend testing is essential in construction because it tests the strength and flexibility of steel reinforcing bars to ensure that, in buildings and infrastructure, the forces acting on the steel reinforcing bars will not compromise the structural integrity. In automotive manufacturing, the tests ensure the manufacture of lightweigt but stiff panels and frames, guaranteeing fuel efficiency and passenger safety.
Bend testing, in turn, is deeply embedded in the aerospace industry to test the strength of modern composites such as carbon fiber-reinforced plastics, which are generally preferred for lightweight aircraft of maximum performance. From bend tests, data are available to prove the reliability of the material and demonstrate its compliance with international safety standards, which are all-important for certification. Beyond their traditional use, bend tests today help push the new frontier in nanotechnology, testing the mechanical properties of materials at microscopic scales, ensuring their practical functionality and durability in electronic, biomedical, and energy storage innovations.
In this manner, industries can actualize sustainability and performance through the correct material selection, product longevity, and responsible innovation, facilitated by precise testing techniques.
Types of Bend Tests
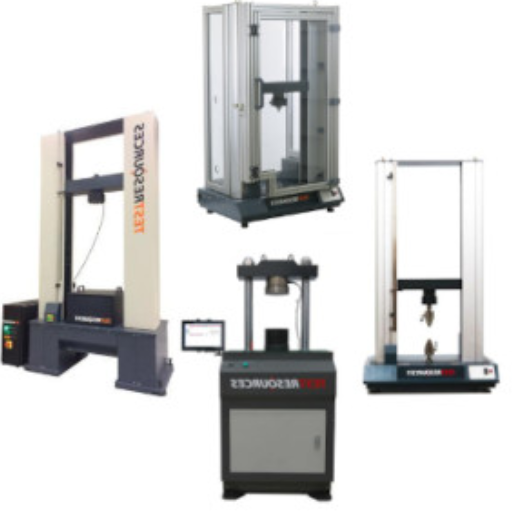
Flexural Tests: What They are and What They do
One of the primary methods for testing the strength and deformation behavior of a material subjected to bending forces is the flexural test. A flexural test mainly elucidates the mechanical properties under stress, such as flexural strength, flexural modulus, or resistance to cracking under the test. Generally, the specimen is placed on a test fixture and loaded until it develops a bend or fracture. Hence, flexural tests serve as crucial tests, as they provide precise guidance on how well a material will behave in load-bearing applications, particularly in engineering, construction, and manufacturing.
The processes of the flexural test have recently been enhanced to increase accuracy and speed. For example, deformation data can now be recorded in real-time with greater precision using a high-resolution sensor, allowing engineers to carry out more precise analyses on complex materials, such as composites and polymers. Developing sustainable materials that are stronger has been key, allowing industries to innovate with structural design while reducing environmental impact. Whether it is concrete beams for infrastructure projects or flexible polymers, flexural testing is undeniably essential for ensuring safety, longevity, and quality in many applications.
Side Bend vs. Guided Bend Tests
While conducting a comparative study of side bend versus guided bend tests, their methodologies, applications, and potential advantages in assessing material behavior under stress must be understood. Side bend tests assess the ductility and soundness of welds by bending the specimen sideways to reveal any internal defects, such as cracks and voids. This method is particularly applicable when considering thicker materials, as their internal quality needs to be verified to avoid structural weaknesses.
On the contrary, guided bend tests are another procedure in which a specimen is bent to a particular angle while being guided by a fixture to assess the total quality and ductility of the weld. Hence, this provides a controlled and thus accurate measurement, seeking consistency in testing that meets industry standards. The guided bend test will perform its duties when instances requiring uniformity and repeatability arise, for example, when certifying welders or ensuring that welding procedure specifications meet regulatory requirements.
This is the ground for the testing types mentioned above: internal imperfection detection is more effective with a side bend test, especially in materials subjected to heavy loading. In contrast, a guided bend expects the workpiece to be bent to a particular angle to pass the test, serving as a more rigorous measure of quality. Depending on the type of material, usage environment, and the objective for the testing procedure, either of these may be used.
Comparison Between Bend and Flexural Test
Bend and flexural tests are typically performed to evaluate the mechanical properties of materials, but they differ in their focus and testing methodology. A bend test mainly checks a material’s ability to plastically deform without cracking under stress. Being mostly carried out on metals, such tests are essential for evaluating ductility and detecting surface or internal imperfections that can hinder performance when these metals are applied in critical applications.
Flexural tests, for instance, are usually associated with rigid materials such as ceramics, composites, and polymers. The tests measure a material’s resistance to bending forces, providing key data on flexural strength and modulus of elasticity. Flexural strength indicators express the tensile stress that a material can withstand before it fails, thereby indicating the material’s operational capability when working under load in a structural capacity.
Advanced technologies are highlighted in recent learning as improving data accuracy during these tests. From these new systems, one can name laser measurement systems and Digital Image Correlation (DIC) for measuring strain and deformation during testing. These data indicate that materials with high flexural strength are suitable for applications that require high stiffness and the ability to carry loads, such as aerospace components or infrastructure materials.
Making these tests understandable strengthens one’s ability to determine which tests are suitable for given material types, with respect to the application requirements and the performance parameters envisioned. The ductile metals undergo bend tests, while the brittle materials undergo flexure. The intersection of tradition with new approaches is what gives dependable analyses and informed decisions on material performance.
Components of a Bend Test Machine
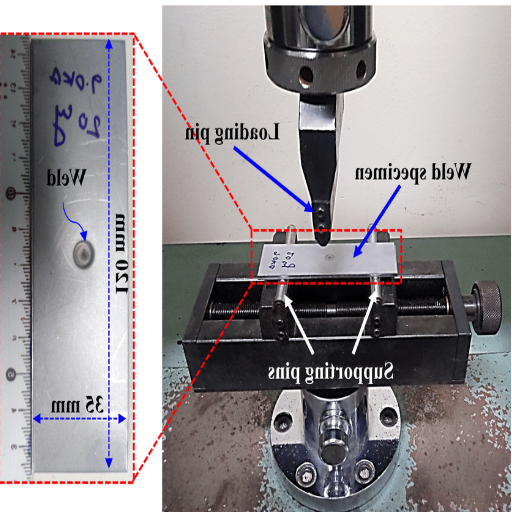
Bend Tester Aids in Understanding
A bend tester is a necessity for evaluating materials in terms of their flexibility and ductility, as well as how they deform under bending stress. The core components of the tester work in a coordinated manner to enable the tester to develop test results accurately and consistently.
Loading Mechanism: It applies precise forces, depending on the type of machine, such as hydraulic, pneumatic, or mechanical. The application of forces can be adjusted to accommodate significant variations in the strength and thickness of the test materials.
Support Fixture: It secures the material during the test; usually, there are two span adjustments to accommodate different sample widths and lengths. Hence, the material placement in a fixture must be precise and accurate for optimal results.
Load Cell/Sensors: This type of force measurement instrument would be highly accurate when the force is applied during the entire testing process. This action integrates the data into an evaluation for determining the yield points, ultimate strength, and bending limits.
Data Acquisition System: This system would acquire, process, and record the primary metrics of load, displacement, and bending angles, often integrating with a software package capable of supporting thorough analysis, report generation, and visualization of test results.
Deflection Measurement Tools: These tools measure the movement or deflection of a specimen during bending. Very precise measurements of deflection will be employed to correlate stress versus strain and to determine the deformability of the materials under applied loads.
Control Panel/Software Interface: The modern-age bend tester comes equipped with an adaptive interface or software providing operators with the ability to assign a test, view data live, and record results. Advanced options may include customizable test protocols, automation features, and in-process graphing.
The interaction between these components thus enables a bend tester to conduct full material characterization, respecting standardized protocols such as ASTM and ISO requirements. With the making of the testing machines, it is now a multipurpose instrument across industries, such as construction, automotive, and aerospace, where the mechanical properties of materials are tested to render reliability and safety to a product.
Fixtures and Their Role in Testing
Fixtures play an indispensable role in maintaining test reliability and reproducibility by holding samples in place during mechanical testing. They are designed to accommodate the variability of sample shapes, sizes, and materials, thereby minimizing the risk of slippage or misalignment that could otherwise lead to erroneous test results. Advanced-level fixtures may have adjustable accommodations to different test standard requirements and are therefore used in conjunction with industries such as aerospace and construction, where precision is crucial.
They are designed using high-grade materials, such as stainless steel or aluminum alloys, to impart toughness and foul resistance against numerous tests. The application of a bend test fixture, for example, provides uniform support and distributes force evenly across the sample per standard procedures. Additionally, features such as quick-change parts and a modular design have been developed to maximize workflow and minimize downtime during and between tests. These advancements serve to enhance the material testing efficiency without jeopardizing the reliability and precision that these critical sectors demand.
Hydraulic Systems in Bend Test Machines
The hydraulic system plays a significant role in the performance and accuracy of the bend test machines. Hydraulic systems generate the bending or requisite deforming force exerted on a piece of material under controlled conditions through pressurized fluid. Generally, a hydraulic system in a bend test machine comprises pumps, control valves, actuators, and reservoirs, all of which operate in harmony to ensure smooth functioning.
These days, hydraulic systems are designed for utmost accuracy in force application and strain control. Highly developed load sensors and feedback systems monitor load application and continuously adjust the system’s output, ensuring the reproducibility of results across multiple test cycles. Further improvements in hydraulic-fluid technology, coupled with advancements in using high-strength materials for hydraulic equipment, have, in fact, contributed to enhancements in the systems’ durability and efficiency. The systems, now equipped with the capability to withstand higher working pressures, can test materials of greater toughness while maintaining stable performance.
To meet industry demands, modern bend testing machines feature customizable hydraulic setups. This customization enables users to align their systems precisely with materials or test standards, ensuring a perfect match with application requirements. With enhanced intelligent monitoring systems capable of operation, fewer personnel hours are needed, thereby reducing human error and improving work ethics and machinery reliability, which is crucial in the aerospace, automotive, and construction material testing industries.
Standard Test Methods for Bend Testing
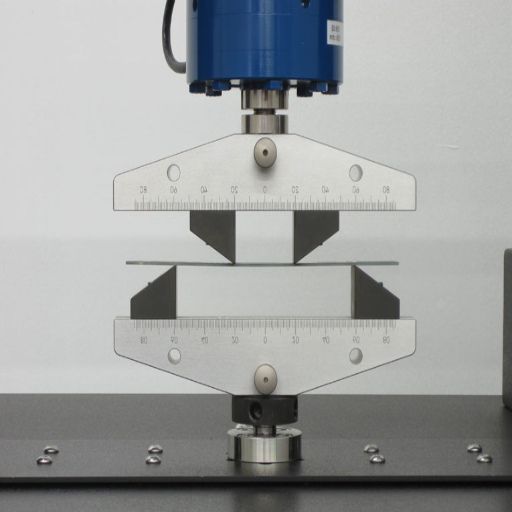
Bend tests with ASTM Standards
ASTM has established several standards for bend testing to assure consistency and reliability in the industry from one branch to another. Among these standards, ASTM E290 is the premier one, which specifies methods for testing the ductility and strength of metallic materials — guided bend and free bend tests. This standard specifies testing parameters, such as the bend angle, specimen dimensions, and minimum radius, to effectively measure the material under stress.
A further specification widely recognized and used is ASTM A370. This specification utilizes the bend test to assess the ductility and resistance to fracture of steels, particularly for reinforcing bars and structural steel.
The other primary established test method for flexural strength testing of ceramic materials is ASTM C1161. This procedure, in manufacturing settings that rely on high-performance ceramics, is crucial in determining whether a technique can be applied in demanding applications.
The standards, of course, must describe reproducibility and precision of data collection methods. For example, they specify particular formulas for calculating bending stress and further require the mandatory documentation and reporting of results. Through adherence to standard procedures, industries are able to maintain greater control during manufacturing to produce finely tuned products with a range of performances suitable for extraordinary applications.
ISO Standards and Compliance
Complying with ISO standards ensures that products or processes meet international quality requirements regarding safety. ISO comprises standards that cover a wide range of industries, including manufacturing, technology, and healthcare, thereby ensuring that products are safe, efficient, and reliable. Organizations that now build with ISO can enhance their product durability and performance while gaining a competitive advantage in global markets.
For example, ISO 9001 focuses on quality management systems and can therefore be used to help corporations improve their business operations and enhance customer satisfaction. ISO 14001 ensures that organizations implement aspects of environmental management with objectives that aim to reduce their ecological impact and promote the sustainable use of resources. It aids in transparent reporting and reduces the incidence of errors while contributing to sustained operational excellence.
Recent data demonstrate how ISO compliance contributes to efficiency improvements and cost reductions. Companies that implement ISO frameworks generally report higher productivity and process improvements. It creates an environment that facilitates international trade by ensuring compatibility and interoperability between products and systems. Through this comprehensive approach, it supports ensuring compliance with regulations and instilling trust in customers and stakeholders who believe the brand prioritizes both quality and sustainability.
Common Test Methods Explained
In industries, standard testing methods are almost indispensable for ensuring the quality, safety, and reliability of a product. Having performance parameters tested under standardized procedures ensures that an item meets the set standards. Mechanical testing, for instance, measures strength, durability, and resistance to stress, among other properties. Tensile testing, for example, measures the force required to break a material as it is stretched; compression, on the other hand, tests the material’s ability to bear loads without deformation.
Environmental testing is another critical category that simulates real-world conditions to determine how products behave over a specified period. Examples of these include temperature cycling, humidity testing, and salt spray testing, each of which determines resistance to environmental forces such as corrosion or extreme temperature. Electrical tests are another good-purpose test when dealing with electronics, wherein they examine factors concerning insulation resistance, circuit integrity, or power consumption.
Functional testing for software and digital products ensures that the system behaves as intended and addresses any bugs and usability issues before release. Chemical analysis is used to help validate the composition and purity of substances in pharmaceuticals, materials, and food.
These test methods confirm product specifications through accuracy and repeatability, while minimizing the risks of failure, thereby reducing costs associated with recalls and enhancing consumer confidence. Using strong testing processes, companies can compete afloat these days while conforming to global standards.
Applications and Industries Utilizing Bend Test Machines
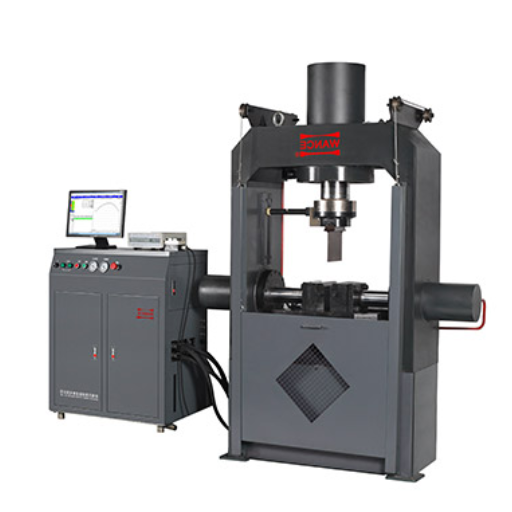
Welding and Fabrication Industries
In my view, bend test machines play a crucial role in ensuring the structural integrity and reliability of materials in the welding and fabrication industries. Putting materials through these machines simulates the types of stress and strain that a material may experience in actual practice, helping me to verify weld quality and detect any possible defects, such as weak points or cracks. This, in turn, ensures that strict industry standards are met and guarantees the durability of the product.
For me, the performance of the bend tests during welding is a design step to avoid failure upfront. Whether it’s metal, alloy, or composite, I recognize the importance of detecting inconsistencies at the earliest stage of the production process. Bend testing enables the evaluation of ductility, flexibility, and functional performance of welded joints, which is particularly crucial in projects related to critical sectors such as construction, automotive, and aerospace.
One aspect I particularly appreciate about this bend testing machine is how efficiently it facilitates the quality control process. The downside of this testing is that very little time and resources are allocated to performing the tests, thereby reducing the chances of going into rework or, worse still, into recalls. By interfacing these technologies, I ensure the production of high-quality products that comply with safety regulations and can be relied upon to meet practical application demands, thereby creating reliability and longevity for players and stakeholders.
Building and Structural Testing
When construction and structural testing are the matters at hand, I seriously adhere to advanced testing procedures and equipment to assess the integrity or reliability of materials. For instance, good-use bend test machines can effectively test the strength and flexibility of construction materials such as steel and reinforced concrete. Such tests assess how the materials behave under pressure, simulating real-life scenarios, so that the material fulfills both safety regulations and structural requirements of their respective applications. The approach instills confidence in material performance while simultaneously ensuring that, through material behavior, brighter, longer-lasting, and stronger construction attempts are possible.
Through testing structural elements, I can identify potential weaknesses earlier in the development cycle. Such a stance would put the unexpected failure or expensive rework far in the future. With tensile testing and fatigue testing machines, I have gained more knowledge about how materials behave over time and under various loads. The obtained data is invaluable in optimizing designs and ensuring that contract undertakings conform to specifications and the client’s expectations.
The ultimate goal of construction and structural testing is to maintain quality and safety at the highest level possible. With the latest technology and strictly standardized testing procedures incorporated in my system, I can confidently provide assignments that not only comply with regulatory requirements but also surpass all expectations set by clients and stakeholders. This on-time delivery that approaches quality builds trust and guarantees unparalleled success on every endeavor.
Aerospace and Automotive Applications
Based on my experience, these two applications are areas where specifications, innovation, and scrupulous testing come together. To ensure the structural integrity and safety of these materials, I dedicate my efforts to utilizing the most advanced materials testing and simulation techniques suitable for these industries. These airplanes, for example, undergo various tests for structural fatigue and non-destructive evaluation under thermal stress conditions to corroborate their capacity to perform in unusual environmental conditions, such as high-altitude pressures and temperature fluctuations. Were it not for such processes, one could compromise on either the safety or cost aspects of an aircraft design.
Likewise, I engage in crashworthiness analysis, durability analyses, and the implementation of lightweight materials in the automotive sector, aiming to improve performance while satisfying safety regulations. With tools such as finite element analysis and real-time data monitoring, I contribute to the development of safer, more fuel-efficient vehicles that meet the ever-changing market demands. Whether it’s improving aerodynamics in aircraft or enhancing energy absorption in car structures, I take a holistic and detailed approach to addressing unique issues in these sectors. My unwavering commitment to quality and innovation ensures that projects in both fields meet and often exceed the required specifications and performance criteria.
Frequently Asked Questions (FAQs)
What Is a Bend Test Machine and How Does It Work?
A bend test machine is, in a way, a kind of testing apparatus set up to determine the bend strength and ductility of any material. In many instances, this involves the application of one or more types of testing methods, such as 3-point bending or 4-point bending tests, so that the specimen’s behavior under bending stress can be observed. Based on the application of a load to the specimen up to a point where the specimen deforms or fractures, an engineer can examine its elastic and plastic properties. In manufacturing and quality control, these machines are used to verify if a material meets standards such as ASTM and ISO. Weldments and composite materials are of particular concern in the manufacturing and construction industries.
What Are the Different Types of Bend Test Applications?
Bend-test applications span a wide range of industries, including construction, aerospace, and manufacturing. Typical materials include metal, plastic, ceramic, and composite materials, which are tested for flexural strength and modulus of rupture. Different types of bend test fixtures are designed for various specimen configurations, such as destructive weld testing. Universal testing machines can also be used for bend tests, given their versatility in testing multiple materials and fulfilling different needs. Engineers then use the results to adapt materials for their final applications, taking into account the stresses they will be subjected to during operation.
How do I prepare a Bend Test Specimen?
A vital factor in preparing a test for a bend test is the dimension and material properties of the specimen. Specimens are typically cut to sizes and shapes as required by the test procedure being used. Thus, for instance, ASTM prescribes dimensions for a 3-point bend test specimen to allow the standardization of testing results. Specimen preparation is of utmost importance for obtaining accurate measurements of bend strength and flexibility. Given this, it is essential to consider the material being tested and assess whether it is ductile or brittle, as much of this will depend on the variation in performance. A smooth surface finish can prevent any irregularities during the test.
What Are the Standard Test Methods for Bend Testing?
The bend test media define the requirements for the test fixture setup and load application according to ASTM and ISO standards. Typically, the test methods randomize a load cell and dual extensometers for force and deflection measurements, respectively, thus guaranteeing the highest accuracy during measurements. The widely applied 4-point testing method is typically used for materials with better flexibility, but it is also suitable for other applications. Following the testing methods ensures consistent results for proper evaluation of materials and comparison with different testing systems.
What Is the Importance of Bend Test Fixtures?
Bend test fixtures are crucial for obtaining precise and repeatable bend test results. These fixtures serve to hold the test specimen safely while an offloading is applied under a controlled load, the main aim being to weigh the flexural properties. Different bend fixture arrangements, whether for 3-point or 4-point tests, greatly influence the results. Then, to some extent, using the correct bend fixture reduces the number of variables that could lead to inconsistent data. An accuracy that is paramount when the test is done for quality control purposes, where a material must conform to a given level of performance before being used for construction or manufacturing processes. The fixture design also significantly impacts the ease of specimen preparation and testing.
How Does Bend Testing Relate to Quality Control in Manufacturing?
In manufacturing, bend testing serves as a fundamental quality control measure, as it is designed to assess the mechanical properties of materials used in products. Manufacturing bend strength and ductility testing aim to ascertain that the material conforms to a particular specification needed for safety and performance. They are of particular importance when the material is used for structural purposes, where any eventuality could lead to dire consequences. While testing can also be done on materials coming from different batches to check for consistent properties and variation properties, it is equally important to implement a stringent bend testing regimen to ensure quality and reliability in every final product.