Like all metals, welding stainless steel requires understanding its unique features to deliver robust welds. Its superb corrosion resistance and shiny finish make it popular with automotives, the medical industry, and construction. Welders, however, face formidable challenges due to the need to control heat input, avoid overheating, manage contamination, and prevent warping.
This guide covers everything you need to know to tackle stainless steel welding confidently. We will analyze stainless steel types for their welding capability, tackle the most critical methods such as TIG, MIG, and stick, and the best tips for excellent results. Every professional and novice willing to master the art of welding will find the guidance they need. After reading this article, you will understand the tools, techniques, and best practices required to weld stainless steel successfully. After reading, you will be empowered to take on your next welding project successfully.
What Are the Best Methods for Welding Stainless Steel?

Stainless steel and its alloys have prompted the development of various welding technologies. The most preferred techniques stem from the specific stainless steel grade utilized alongside its related project specifications while considering the controlled environment. TIG (Tungsten Inert Gas) welding is the best option to nurture intricate and delicate welds for high-precision welds on thin materials. MIG (Metal Inert Gas) welding is another effective method that offers ease of use and fast welding speeds, which are usually beneficial to thicker materials or industrial projects. Though not conventional for stainless steel, Stick welding can be practical in outdoor or uncontrolled settings. Attaining the best results is fostered by the right filler materials, controlled heat, and a clean surface before welding.
TIG Welding: The Preferred Method for Stainless Steel
TIG welding’s main advantage is the accuracy and control it offers for all stainless steel applications. This process utilizes a non-consumable tungsten electrode for the arc. At the same time, an inert gas like argon shields the weld area to prevent contamination, making it suitable for delicate and high-demand tasks. Focusing on aesthetics without warping thin stainless steel sheets further enhances the appeal TIG welding brings to thin sheet work.
Practical TIG welding requires the settings to be configured with low amperage and steady torch movement across the weld line. To ensure compatibility and strength, welders apply a stainless steel filler rod. Also, cleaning in conjunction with removing the oxide layer and any contaminants aids in surface preparation and helps avoid porosity as a defect. Even though the skill level and time required to perform TIG welding are higher than those required for other welding methods, the durability and polish achievable through TIG make it the preferred technique for high-performance stainless steel welding.
MIG Welding Stainless Steel: When and How to Use It
MIG welding is most appropriate for my projects when I have to use thicker stainless steel plates and necessitate speed without compromising the strength of the welds. Considering how reliable the penetration with the welds is during MIG welding, I’m sure the results will be consistent across different attempts. To get the best outcomes, I use a shielding gas mixture of argon and CO2 to limit the occurring oxidation and spatter. As with any welding process, pre-cleaning surfaces of contaminants are of utmost importance since they help achieve a clean weld bead and reduce defective chances to the absolute minimum. While I appreciate the polished finishes of TIG welding, I find myself reaching for the MIG welding system with increased productivity demands. Although it can sometimes be imperfect, enjoy how TIG welding works efficiently.
Stick Welding and Arc Welding Applications for Stainless Steel
Among all welding methods, stick welding or shielded metal arc welding (SMAW) is the most portable and effective for stainless steel. It can be performed outside and on dirty surfaces. The type of welding performed uses electrodes coated in flux, which reduces oxidation in the weld pool. Stick welding is best for maintenance and repair work. It is also great for applications requiring thick stainless steel materials.
Arc welding, which includes TIG and MIG welding, is known for its accuracy and offers a high degree of flexibility. Nonetheless, in terms of stainless steel stick welding applications, the focus shifts towards simplicity and price, especially in cases where equipment is not too advanced. This process performs exceptionally well in strong and durable welds needed for pipelines, construction, and structural components.
When performing stick welds with stainless steel, the electrodes employed should match the grade of stainless steel used. This ensures strength and resistance to corrosive elements at the welds. Adequate surface preparation is also very important since it greatly reduces the number of defects and helps in providing clean welds. Due to its dependable nature, stick welding is a popular choice for projects demanding high durability and versatility.
What Equipment Do I Need to Weld Stainless Steel?
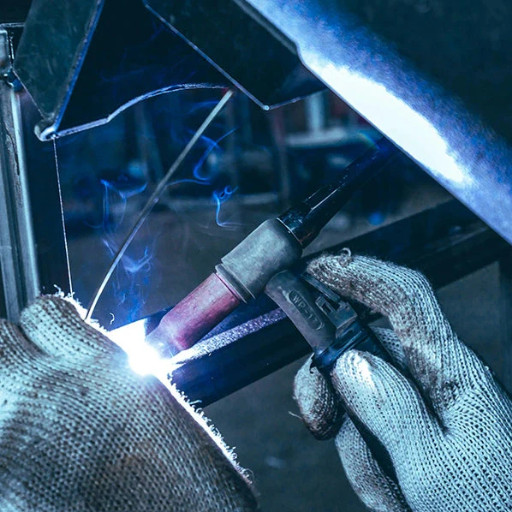
Welding stainless steel requires the following items:
Welding machine: Use a MIG, stick, or TIG welding machine suitable for stainless steel.
Electrodes or filler rods: These are used to weld stainless steel of the same grade as the material being welded and are matched to the stainless steel electrode or filler rod.
Shielding gas: For TIG or MIG welding, a shielding gas such as argon or an argon-helium mixture should be used.
Protective gear: Personal protective equipment (PPE) includes welding helmets, gloves, flame-resistant clothing, and safety boots.
Clean workspace and tools: To ensure the workpiece is contaminant-free, required materials include stainless steel brushes, grinders, and clamps.
These tools and materials are handy for stainless steel when a strong, clean, and corrosion-resistant weld is required.
Essential Welding Machines for Stainless Steel
Meeting the requirements of any job involving stainless steel welding begins with choosing the right welding machine. Here are some of the most useful machines that have received favorable reviews:
TIG (Tungsten Inert Gas) Welders: With stainless steel, welding must be precise, and TIG welders such as the Miller Diversion series or the Lincoln Electric Square Wave can meet this requirement. These machines also control the heat input, which reduces the possibility of discoloration or warping.
MIG (Metal Inert Gas) Welders: MIG welders such as the Hobart Handler and Everlast PowerMTS can efficiently weld thinner stainless steel sheets. A mixture of shielding gases, such as argon with a small amount of carbon dioxide, ensures smooth operation.
Stick Welders (Shielded Metal Arc Welding): Stick welders such as the ESAB Rebel or Lincoln AC/DC series are very effective for more rugged or outdoor applications. In addition to being versatile, these welders are also helpful in uncontrolled environments.
Regardless of the option chosen, these machines guarantee the precision required to handle a variety of welding scenarios. As a result, they can be used for efficient stainless steel welding.
Choosing the Right Shielding Gas for Stainless Steel Welding
Choosing the right shielding gas is very important for achieving high-quality stainless steel welds. It is essential to consider the process of welding and the expected results. In the case of Gas Tungsten Arc Welding (GTAW/TIG), the use of an operon almost exclusively guarantees stability and control of the arc; for GMAW/MIG, a blend of Argon with carbon dioxide is the mixture of choice, usually 98% Argon and 2% CO2. In this blend, oxidation is low, which allows for stable arc welding and intense penetration. In some specialized MIG procedures, adding helium (90% He, 7.5% Ar, 2.5% CO2) makes the process applicable for thick metals as it adds heat. The shielding gas mixtures described minimize contamination while providing solid fundamental welds that meet the expectations for projects involving stainless steel.
Stainless Steel Wire and Filler Material Selection
Choosing the correct wire and filler material for welding stainless steel is very important. It directly impacts the amount of base metal used, the application intended, and the properties desired from the weld. Stainless steel wires commonly employed include ER308L, ER309L, and ER316L. ER308L caters to servicing 300-series stainless steels, whereas ER309L has superiority over welding dissimilar stainless steels to carbon steels. ER316L dominates in places like the marine and chemicals industries where advanced resistance to corroding is valuable, like in a corrosive resistant environment.
While choosing filler materials, select pieces that will harmoniously go with the base without causing cracks or rusting. They are also known as low-carbon fillers and are marked with “L” in their name, further weakening carbide formation and sustaining anti-corrosive properties. Cleaning the base material in advance and using the right alloy that matches the base metal’s type improves the effectiveness and durability of the weld. Follow the guidance of a trained professional in conjunction with the manufacturer’s instruction to ensure maximum success for the project alongside industry standards of choice.
What Are the Common Challenges of Welding Stainless Steel?
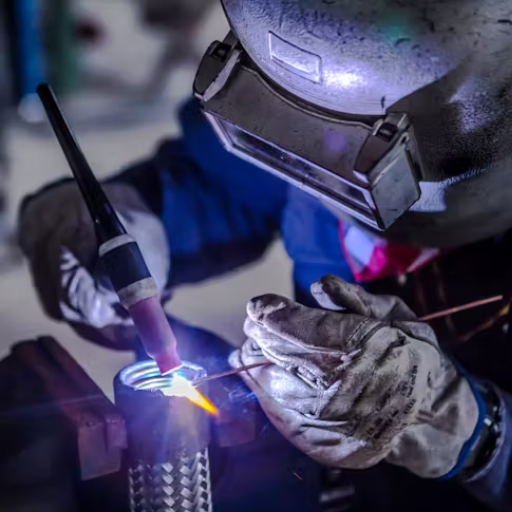
Stainless steel, as with other metals, presents unique challenges that require proper attention. One prominent challenge in welding is managing the heat input. Excess heat results in distortion, warping, or loss of the material’s protective qualities, such as its corrosion resistance. Managing chromium carbide precipitation also poses a challenge during stainless steel welding. Chromium carbide precipitation can lead to intergranular corrosion and occurs during improper cooling.
Along with other metals, stainless steel is prone to thermal expansion. With its elevated thermal expansion rate relative to other metals, the likelihood of cracking increases during the welding process. Proper material preparation, cleanliness, and appropriate welding techniques can achieve strong, durable welds.
Preventing Heat Input Issues When Welding Stainless Steel
When controlling the parameters and techniques while welding stainless steel, care must be taken to prevent any issues with heat input. Excessive heating can result in thermal distortion and reduce the material’s ability to resist corrosion. A low heat input method, like controlled amperage TIG welding, should be used to prevent these issues. Additionally, the proper choice of filler material and constant and steady welding speed can minimize carbide precipitation. Pre-cleaning weld surfaces to remove contaminants and employing appropriate shielding gases such as argon or helium also help achieve the desired quality for the welds. Furthermore, post-weld treatments can help to negate the effects of heat and restore the material’s ability to resist corrosion. Using careful control and thorough preparation, most issues related to heat input can be effectively avoided.
Addressing Warping and Distortion in Stainless Steels
I concentrate on heat input during welding to adequately control warping and distortion in stainless steel. To avoid overheating, intermittent welding, and smaller weld beads are used. I use adequate clamps and fixtures to hold the material in place to mitigate movement during cooling. Furthermore, counterbalancing welds on either side of the joint helps balance distortion due to thermal stress. Optimized dimensional fill materials and their sequences also help maintain stability. I can effectively mitigate the risks of warping by employing these techniques, ensuring the required results are achieved.
Avoiding Contamination in the Weld Pool
The cleanliness of the weld pool is critical to its integrity as well as its overall quality. To avoid these risks, the base material must be cleaned with wire brushes or solvents—removing oil, dirt, rust, and other impurities—before the welding begins. Moreover, the filler materials should be clean and in good condition, as mold and dust can be contaminated by improper storage. Utilizing the correct type and shielding gas flow rate enables the weld pool to be oxidized at minimal exposure to the outside air. Proper equipment maintenance, like changing gas nozzles and looking for gas leaks, also significantly impacts contamination reduction. A combination of prevention neglects optimal results but does maintain a clean weld pool.
How Does Welding Stainless Steel Differ from Carbon Steel?
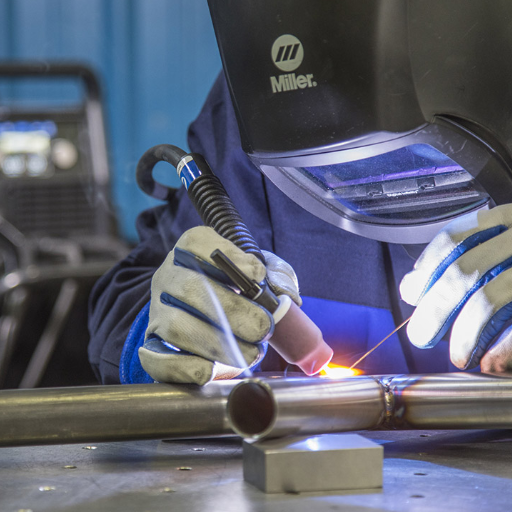
The differences in the composition of the materials, including their potential difficulties, distinguish welding stainless steel from carbon steel, along with the thermal properties. For instance, stainless steel has lower thermal conductivity and more significant thermal expansion; thus, it is more prone to distortion and warping during thermal welding. Furthermore, its composition also includes chromium, which forms a protective oxide coating. However, this also makes the material more susceptible to sensitization and corrosion when subjected to elevated temperatures. It requires specific control of heat input, specific stainless steel fillers, and sometimes backing gases to maintain the weld’s nitrogen level and avoid contaminating the stainless steel structure. In auto fabrication, on the other hand, carbon structures are more straightforward to weld due to lesser chances of warping and corrosion complications.
Key Differences Between Stainless Steel and Mild Steel Welding
Material Properties: Unlike mild steel, which is susceptible to corrosion due to its higher carbon content and lack of chromium, stainless steel has chromium, making it corrosion-resistant. Furthermore, chromium is present in stainless steel, giving it resistance against corrosion, while in mild steel, it is absent, making it prone to rust when in contact with moisture.
Mild steel is readily welded using various methods, including MIG, TIG, or stick welding, as it is less sensitive to heat. Unlike stainless steel, which is sensitive to heat with specific welding requirements, mild steel can be welded easily and is less sensitive to various welding methods. Welding stainless steel requires careful gentleness with the heat and has particular requirements like controllable heat input, certain grade filler metals, shielding gas like argon to prevent oxidation, and others.
Cast steel handles heat better and is more adaptable without bending or changing shape during welding. This is achieved through evenly distributed heat, which mild steel can achieve. Unlike stainless steel, mild steel has better thermal conductive properties, which enable it to distribute heat evenly.
Unlike mild steel, welded stainless steel retains corrosion resistance, enabling it to function properly in harsh environments. On the other hand, a lack of proper welding could facilitate sensitization, which does cause some reduced performance. Compared to stainless steel, mild steel is less corrosion-resistant and requires extra coatings or treatments to defend against rust, especially in acidic or humid conditions.
Cost and Accessibility: Welding stainless steel is more expensive than welding mild steel due to the required tools, gases, and filler materials, as well as additional welding methods. On the other hand, welding mild steel is cost-effective and readily available for use in numerous industrial applications.
Austenitic Stainless Steel Welding Techniques
While welding austenitic stainless steels, it is best to use methods that conserve heat to minimize deformation and preserve corrosion resistance. In the case of tungsten inert gas, argon or argon-helium mixtures are excellent choices as they protect the weld pool, and appropriately balanced alloyed filler metals ensure the weld’s strength and integrity. I make sure to scrub the surface to remove contaminants because any remaining could result in weld flaws as a result of post-cleaning. So, controlling interpass temperatures is equally essential as controlling ductility and unneeded heating, which can result in sensitization. While using TIG, MIG, and even modern methods, I have achieved the best results when precision and control over the outcome are prioritized.
What Are the Step-by-Step Basics of Welding Stainless Steel?
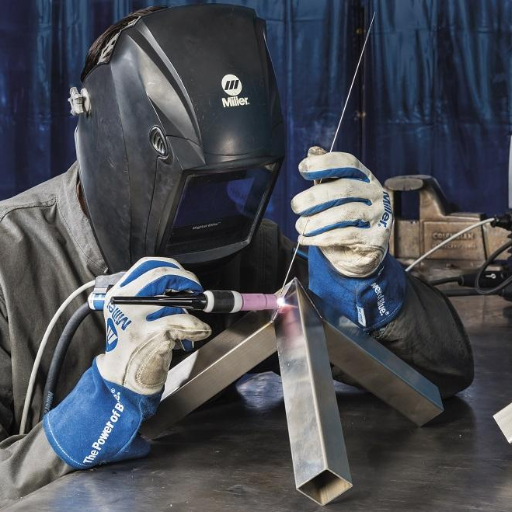
Pick the Appropriate Tools and Filler Metals: Choose the appropriate welding process, like all specialized works. In this case, it can be either TIG or MIG. Ensure the filler metal complies with the base metal’s suitability, strength, and correlation grade requirements.
Prepare the Surface: Ensure the stainless steel surface is free of dirt, grease, and oxidizing substances. A stainless steel brush and a solvent for pre-cleaning to lower contaminant levels will do.
Setting Up The Shielding Gases: Inert gases like Argon or argon with helium can be used in the weld pools to prevent oxygen and nitrogen from entering and causing defects (like porosity).
Control Heat Input: Excessive heat can cause warpage, changes in color, or corrosion resistance. If possible, use techniques like pulse welding to monitor interpass temperatures.
Apply Correct Welding Techniques: Proper angles and a steady hand for every torch or gun set will go a long way toward consistency and desired outcomes. Do tack welds first to keep the parts attached, and then proceed to put full welds on the joint.
Post-Weld Cleaning and Polishing: When the work with welds is done, clean the vicinity of the weld with more specific tools, like brushes and stainless-steel pickling paste, to get rid of oxides and unsightly corrosion retro-resistant and ensure that it is smooth with no harsh or unsightly edges.
Proper Preparation of Stainless Steel for Welding
Cleaning the surface and adequately preparing stainless steel for welding is vital when aiming for solid and corrosion-resistant welds. Here are the key techniques:
Surface Cleansing: Maintaining steel surfaces is relevant to conducting welding. Be sure to use the best degreasers to remove grease and other foreign substances. If certain contaminants are not effectively eliminated, alcohol-based cleaners or acetone can be utilized. The surface must be dry before proceeding to the next stage.
Oxiide Layer Removal: Dedicated stainless steel grinding tools should be used to remove welding area oxide layers (as well as mill scales) accruing on the steel surfaces. Avoid using anything other than these tools since they render stainless steel susceptible to contamination and cross-reactivity.
Surface Contamination Prevention: Eliminating foreign particles or substances (contaminants) from contact with stainless steel becomes useful in cross-contamination prevention. Avoid enabling steel so as to maintain purity free from carbon debris while using specific brushes and tools for this purpose.
Steel Alignment and Joint Reduction: Reduce joint gaps to improve alignment for stainless components. Proper gap-closing enhances precision by improving weld integrity and avoiding gaps.
The inspection is final: It becomes vital to clean the joint along the surface to be welded at first, which undergoes cold inspection. Contaminants, imperfections, and the like should be dealt with before the moment deemed necessary.
These preparatory steps preserve the anti-corrosive attributes of the stainless steel while ensuring proper and enduring welds.
Mastering the Welding Process for Quality Welds
I focus on the joint prep and the actual cleaning process to achieve precise welds. In my case, cleaning means the edges are accurately machined, and oil, rust, and dirt, which weaken the weld, are removed. When welding, I carefully control heat to avoid warping the stainless steel and putting undue stress on the material. After welding, I thoroughly inspect for defects like cracks and incomplete fusion and corrective measures. This range of corrective measures ensures every weld manufactured is strong, durable, and corrosion-resistant.
Post-Weld Treatment for Stainless Steel
Post-weld treatment is critical in preserving stainless steel’s mechanical and corrosion-resistant attributes. One essential procedure is cleaning the weld to tackle heat tints, oxides, and surface contaminants, which significantly weaken corrosion-resistant capabilities. Pickling, which utilizes an acid solution for oxidation layer elimination alongside mechanical cleaning bracing and grinding, does help achieve this goal.
Another vital step in the process includes removing the surface layer, which restores a durable chrome oxide cover that overactively protects stainless steel from rust while ensuring it withstands the elements. Other factors, such as stress relief heat treated or treated on specific stainless steel grades, reduce residual stresses, enhance durability, and fortify resilience.
Proper drying and inspection after treatment are important steps to ensure proper cleanliness and surface treatment. These post-weld treatment practices maximize the welds’ strength and durability in harsh conditions over long periods.
What Tips Can Improve Your Stainless Steel Welding Results?
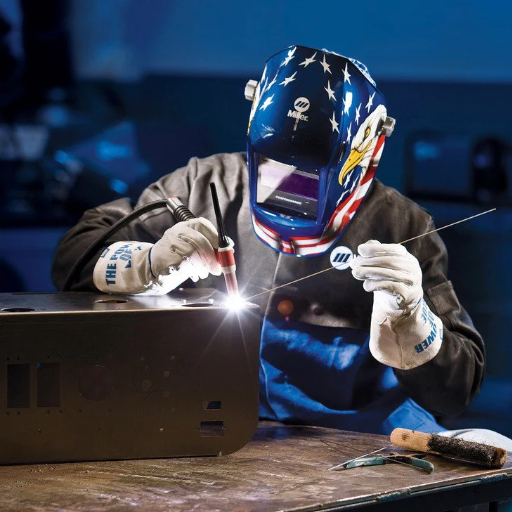
Choose the correct type of filler. The filler material must be equal to or more potent than the grade of stainless steel being welded for adequate strength and resistance to corrosion. Maintain cleanliness. It is required to clean the parent metal by removing any oil, dirt, and grease contaminants as they can all affect the quality of the weld—manage heat input—control it. Use proper heat settings and avoid overheating to limit warping and reduce the likelihood of chromium carbide precipitation, which is corrosive. Employ backflushing. For critical applications, backflushing with argon as an inert gas safeguards the base of the weld from oxidation. Employ correct procedures from ergonomic travel speeds and gun angles to smooth weld surfaces to avoid overheating for better quality. Complete and accurately review the weld. Inspect the weld, remove any existing defects, and carry out post-fabrication processes like grinding or cleaning to enhance the endurance and aesthetic appeal of the weld.
If quality outcomes are desired, consider these best practices when undertaking projects involving stainless steel welding.
Achieving Good Welds: Professional Techniques
Adhering to proven techniques and best practices is necessary for optimal weld quality. To aid your needs, top recommendations have been combined into a concise guide.
Material Preparation: It is recommended that the surface be cleaned first in any welding process. Impurities such as dirt, oil, and rust should never be present. Use a non-corrosive stainless steel cleaner or a brush specifically designed for stainless steel. This will go a long way in preventing contaminants from impacting weld quality.
Use of Shielding Gases: Use shielding gas blends like argon or gas mixtures of argon and helium to shield the weld pool and prevent oxidation. Proper gas flow and sustaining gas sufficiency are also important in protecting the stainless steel structure.
Control of Thermal Input: While integrating the weld with a steel structure, manage the thermal input to prevent overheating. Overheating can lead to disfigurement and color distortion. Setting the correct amperage with intermittent and back-stepping welding techniques will provide a solution to high thermal concentration.
Choosing Electrodes and Filler Materials: Blending base metals with compatible filler materials that maintain those attributes and grade alloys can achieve consistent strength with high resistance to corrosion and tensile forces. For precision during TIG welding, opt for the correct size and type of tungsten electrodes.
The appropriate use of professional-grade tools, the right techniques, and proper planning can greatly improve the strength, aesthetics, and durability of welds. Stainless steel welding is guaranteed to succeed when following these practical steps.
Troubleshooting Common Stainless Steel Welding Problems
Cracking in Welds: Cracking may occur due to excessive heat input and may be associated with high temperatures and stresses on the weld. To avoid this, apply correct preheating. Filler metals must be compatible with the base metal, the welding threshold must not be too high, and cooling rates must be appropriately calibrated. Changes in technique may help relieve internal stress.
Changes in Color or Oxidization: Oxidation is a rusting process caused by the weld material’s too-high temperature. Changes in color or oxidization are often byproducts of overheating and a lack of shielding gas. To maintain cleanliness, ensure proper flow rates, and shield gas use. A reduction in the oxidation potential must also be guaranteed. Post-weld cleaning processes such as pickling or passivation will restore the cleanliness of the stainless steel surface.
Distortion and Warping: Excess heat input to the extent of over-stressing metal may lead to distortion. Use clamps or fixtures to limit the relative motion between the welded components, control the rate at which force is reached with heating, and ensure controlled stitching. Maintaining the current above-set values to cool between passes and reduce warping may be beneficial.
Weld Porosity: Porosity usually occurs due to contamination by grease, oil, or paint gasses shielding the weld, which may be loose and cause poor weld. Ensure the material base is clean and dry, control the gas flow rate, properly shield gas, check hoses for gas leaks, and seal any gaps in connections. The use of pure electrodes will minimize filler materials.
Detection of the weld defects allows one to alleviate some of the problems encountered when welding stainless steel, thereby increasing the reliability of the welds.
How to Choose the Right Type of Welding for Different Stainless Steel Projects?
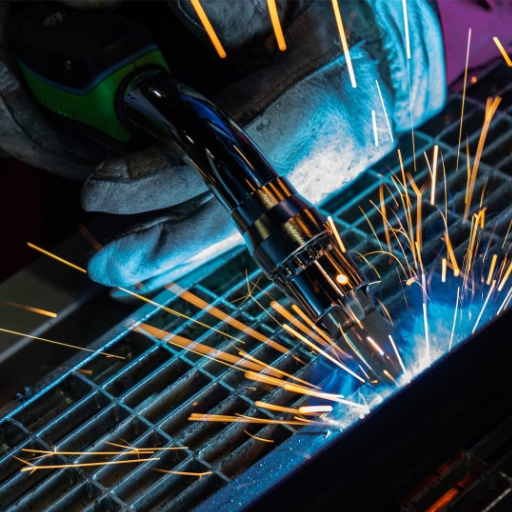
Reflect on the requirements of your task while choosing the appropriate methods of welding for stainless steel:
TIG Welding (GTAW): Because of its precision, TIG welding is best suited for thin stainless steel and clean, controlled welds for projects needing finesse.
MIG Welding (GMAW): Best for heavier stainless steel and faster work rates, MIG welding offers greater ease and efficiency for novice welders.
Stick Welding (SMAW): SMAW is primarily for outdoor use. It is good for stainless steel projects where the work is rugged and needs strength, but appearance is not a primary concern.
Accomplish best results by tailoring the welding method to material thickness, complexity, and desired finish.
Gas Tungsten Arc Welding for Precision Projects
Gas Tungsten Arc Welding (GTAW), commonly called TIG welding, is renowned for producing clean and precise welds, especially where top-notch results are needed. This welding method employs a non-consumable tungsten electrode, an inert gas shield (usually argon), and filler material if required. Its typical applications are welding thin metals, stainless steel, and some exotic alloys because of its control over the heat and weld quality.
Because of the superior aesthetic results that TIG welding yields, it has become a first choice in the aerospace, automotive industry, and art fabrication. However, it demands a level of skill not required in other methods and works at a slower pace than most. The best results are obtained when the surface is clean and prepared, and the machine settings are correct for the material thickness and type. GTAW may not be the most appropriate choice for applications requiring speed or heavy-duty work, but where precision is unrivaled is intricate work.
MIG Welding for Production and Efficiency
MIG welding, also known as gas metal arc welding (GMAW), has always been popular in multi-welding shops due to its fast speed and high firing rate. It is one of the easiest methods to master and is well-suited for projects that require efficiency and high production output. MIG welding can handle thicker materials and large-scale operations more than GTAW. It uses a continuously fed wire as electrode and filler material, significantly increasing productivity.
When completing an MIG weld, I ensure a constant wire feed rate, correct proportions of the contoured gas to protect the base area, and that the metallic bases are clean. Although I must concede that while it lacks the precision of GTAW, the adaptability of MIG welding makes it ideal for aluminum and mild steel when the deadline or demand is high.
Selecting the Best Welding Method Based on Steel Grade
The material’s composition, thickness, and practical application influence the selection of a suitable welding technique for a particular steel grade. MIG welding is most commonly used when dealing with mild steel because it is effective and works with many thickness levels. In contrast, TIG welding excels with stainless steel and other applications where fine details and heightened accuracy are paramount because it has minimal spatter and produces clean, precise welds. Stick welding (SMAW) is thought to be best for high-strength or alloy steels because of its efficiency on thicker sections and less controlled surroundings. No matter the case, the correct filler metal and shielding gases must be employed alongside the steel grade and appropriate preparation to maximize weld quality.
References
Frequently Asked Questions (FAQ)
Q: What is the best for stainless steel welding?
A: TIG (Tungsten Inert Gas) welding is generally considered the best for stainless steel, providing the highest weld quality with minimal distortion. MIG welding is also practical, especially for thicker materials. When choosing a method, consider your material’s thickness, skill level, and equipment availability. Proper welding techniques for stainless steel require more precision than regular steel due to its thermal properties. Remember that stainless steel is a popular building material because of its corrosion resistance, which you’ll want to maintain during welding.
Q: What are some essential tips for welding stainless steel?
A: When welding stainless steel, always clean the metal before soldering to remove contaminants. Use dedicated stainless steel wire brushes to avoid cross-contamination. Control heat input carefully, as stainless steel doesn’t dissipate heat like carbon steel and can warp easily. Use the correct filler metal that matches your base material. Maintain proper shielding gas coverage to prevent oxidation. For thin materials, use tack welds and work in small sections. After welding, allow for adequate cooling and consider post-weld treatments to restore corrosion resistance. These tips for welding stainless steel will help ensure strong, attractive welds.
Q: What are the standard methods for welding stainless steel?
A: The standard methods for welding stainless steel include TIG welding, which offers precise control and is excellent for thin materials; MIG welding, which is faster and suitable for thicker pieces; Stick welding, which works well in field conditions but may not be as clean; Flux-cored arc welding, ideal for outdoor applications; and Plasma arc welding, which is used for automated processes. Each method has specific applications depending on the type of stainless steel, thickness, and project requirements. Your choice should be based on the particular grade of stainless steel you’re working with, as different welding processes may be better suited for austenitic, ferritic stainless, or martensitic varieties.
Q: How does welding with stainless steel differ from other metals?
A: Welding with stainless steel requires special considerations compared to other metals. Stainless steel has lower thermal conductivity, meaning it retains heat longer and can warp more easily. It’s more susceptible to chromium carbide precipitation at high temperatures, which can reduce corrosion resistance. The weld puddle behaves differently, appearing more sluggish than with regular steel. Stainless steel is also more reactive with atmospheric elements, requiring better-shielding gas protection. Different grades of stainless steel (austenitic, ferritic, martensitic) have varying weldability characteristics. Understanding these differences is crucial for successful welding of stainless steel projects.
Q: Can you weld stainless steel without gas?
A: While welding stainless steel without gas using flux-cored wire specifically designed for stainless steel is possible, it’s not the recommended approach for quality results. The flux in these wires creates a shield that protects the weld from atmospheric contamination. However, this method typically produces more smoke and spatter and may result in welds with less corrosion resistance than gas-shielded processes. For optimal results when working with a piece of stainless steel, especially in critical applications, using proper shielding gas such as argon or an argon/helium mix with TIG welding, or an argon/CO2 mix with MIG welding will provide superior weld quality and maintain the material’s corrosion-resistant properties.
Q: What is the best way for beginners to weld stainless steel?
A: For beginners, MIG welding is generally the best way to weld stainless steel as it’s easier to learn than TIG welding. Start with a MIG welding machine set to DCEP (reverse polarity) and use ER308L filler wire for most common stainless steels. Choose tri-mix shielding gas (helium, argon, and CO2) for optimal results. Practice on scrap pieces before attempting your actual project. Begin with clean material and use parameters slightly lower than what you’d use for regular steel. Work in short sections to prevent heat buildup and warping. As you gain confidence, you can progress to TIG welding, which offers more precision and cleaner welds for stainless steel projects.
Q: How do you prepare the stainless steel before welding?
A: Proper preparation is crucial when stainless steel comes to your workbench for welding. First, thoroughly clean the material with acetone or a dedicated stainless steel cleaner to remove oils, grease, and contaminants. Never use chlorinated solvents, as they can cause cracking. Use a stainless steel brush (dedicated only to stainless to prevent cross-contamination) to clean the weld area—bevel edges for thick materials to ensure proper penetration. Fit-up should be precise, with minimal gaps. Tack weld at intervals to maintain alignment during welding. Preheat is generally not required for austenitic stainless but may be needed for some ferritic and martensitic grades. Finally, ensure your workspace is clean and free from carbon steel dust, which can contaminate the weld.
Q: What safety precautions should be taken when welding stainless steel?
A: Standard welding safety measures apply when welding stainless steel, plus some specific precautions. Always wear appropriate PPE, including an auto-darkening helmet, heat-resistant gloves, and non-flammable clothing. Use respiratory protection as stainless steel welding produces hexavalent chromium fumes, which are carcinogenic. Ensure good ventilation or use fume extraction systems. Be aware that stainless steel is an intense heat reflector and retainer, increasing burn risks. Keep fire extinguishers nearby as hot stainless material may not appear hot but can ignite combustibles. Ground your workpiece properly to prevent electrical hazards. When using different welding processes on stainless steel, adjust your safety measures accordingly – TIG welding produces fewer fumes than stick welding but still requires proper protection.