This article will explain PA66 GF30, the most advanced glass fiber-reinforced plastic. You will suppose it is the most sophisticated material, so we will analyze its composition, structure, elastic properties, thermal stability, and advantages over other engineering plastics to appreciate the magnificence of PA66 GF30 more thoroughly. There are many areas where this material can be utilized – automotive, electrical, and industrial. If you are in one of these sectors and looking for guidance, this blog will help you better understand the PP GF30’s properties. Just read this text to begin this technical journey and discover all the possibilities of PA66 GF30.https://pom-material.com/blog/pa66-nylon/
What is PA66 GF30 Plastic, and How is it Used?
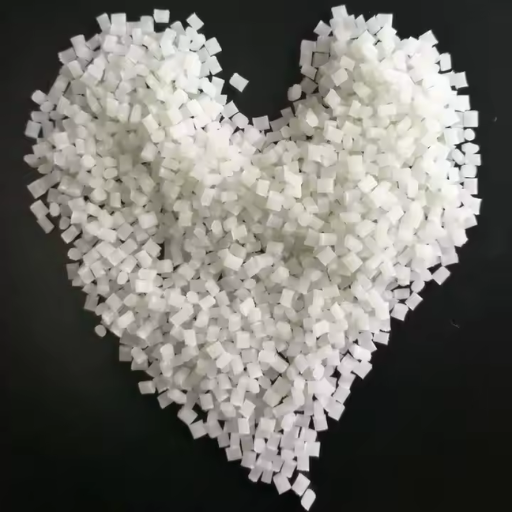
P66 GF30 is a high-end variety of engineering plastic,c, with a significant percentage of glass fiber reinforcement in polyamide 66. As a bonus, it further enhances the performance characteristics of polyamide 66 by adding 30% of glass fibers. It has excellent mechanical stability under sustained load and maintains the desired dimensions with low creep deformation. There is a strong requirement for good strength, better performance, and durability in automotive parts, electrical connectors, industrial equipment, etc, and PA66 GF30 can fulfill these requirements. The ability of PA66 GF30 to meet specific material requirements and such properties makes it very attractive to manufacturers.
Understanding the Composition of PA66 GF30
PA66 GF30, commonly known as polyamide 66 incorporating 30% glass fibers, is a widely used engineering plastic with great mechanical attributes. It is composed of two main ingredients:
- Polyamide 66 (PA66): PA66 is a thermoplastic with impressive mechanical properties, such as tensile and impact strength, resistance to heat, solvents, and abrasion. It serves as the primary matrix of the blend.
- 30 Percent Glass Fiber Reinforcement: Using glass fibers, pleasure 66 GF30’s mechanical features are improved. These fibers, usually chopped or short strands, are evenly distributed throughout the polyamide matrix. The fibers are incorporated as reinforcement for the composite material’s high tensile strength, stiffness, and even dimensional stability.
PA66 GF30 successfully combines the characteristics of glass fibers and polyamide 66, creating a suitable strength, resistance, and performance combination. Its constitutions allow for offering high-quality performance in a range of applications in different sectors.
Typical Applications of PA66 GF30 in Various Industries
I am knowledgeable about technical perspectives regarding the PA66 GF30 ,Through my analytic assessment, I conclude that PA66 GF30 has a broad scope of applications in the automotive, electrical electronics, and industrial manufacturing industries.
Thus, the general PA66 GF30 applications in the automotive sector range from engine covers to other components, such as fuel system parts and air intake machines. The material is suitable for automotive applications primarily due to its high strength and resistance to bending and deformation.
Some applications of PA66 GF30 in the electrical and electronics industry include connectors, switches, and housings. The material also works well because of its heat deflection temperature, which ensures good properties and dimensions even when subjected to high load temperatures.
PA66 GF30 is preferred for machinery components, gears, and structural parts in industrial manufacturing. The elongation at break also helps the material’s general reliability and lifetime because it resists deformation before failure occurs, which is immensely valuable for demanding industrial areas.
The potential uses of PA66 GF30 extend far beyond the examples outlined above. Its unique strength, thermal resistance, and dimensional stability make it a desirable material across various industries. However, PA66 GF30 Tornado C2F should be accompanied by carefully evaluating its technical parameters and the application‘s requirements to ensure performance and durability in the specified application.https://pom-material.com/pa66/
Advantages of Using Glass Fiber Reinforced PA66
The advantages of Glass fiber-reinforced PA66 (PA66 GF30) explain its popularity across several sectors. Some of the key benefits of using Glass Fiber Reinforced PA66 include:
- Increased Strength and Stiffness: The addition of glass fibers into the polymer matrix of PA66 provides an exceptional increase in its stiffness and strength while at the same time increasing its anti-deformation properties. This makes it possible to use PA66 in manufacturing components and parts subjected to high mechanical stresses.
- Excellent Thermal Resistance: Glass Fiber-Reinforced PA66 composites can withstand high temperatures while under load without changing their size or shape. This impressive thermal resistance ensures reliable performance and longevity in demanding applications.
- Improved Impact Resistance: Adding glass fibers to PA66 enhances its impact resistance, allowing its strength to withstand significant stress levels and preventing deformation or failure under high dynamic loads or impact.
- Good Chemical Resistance: PA66 GF30 exhibits good resistance to oils, fuels, solvents, and numerous industrial chemicals. This property also makes it suitable for applications where exposure to various chemical substances is necessary.
- Improved Dimensional Stability: PA 66 reinforced with glass fiber has better dimensional stability, which means it can maintain its shape and size even after adequate time under mechanical and thermal stress. This is important for the consistent and coordinated fit and functional performance relationship where interference fit requirements exist.
Exploring the Mechanical Properties of PA66 GF30

A close examination of the mechanical properties of PA66 GF30 composites considers specific key parameters for achieving appropriate performance for the desired application. The following summary of technical parameters is necessary to appreciate the mechanical properties of this composite material.
- Tensile Strength: This parameter shows the force that can be applied to a material until it breaks under tension. Quite significantly, PA66 GF30 has a high tensile strength, which is a positive characteristic in providing structural stability and mechanical forces stability.
- Flexural Strength: Flexural toughness is the capacity of a material to resist deformation under bending loads without breaking or developing a permanent notch. PA66 GF30’s high flexural strength also supports its resistance to loading and bending stresses.
- Modulus of Elasticity: The modulus of elasticity, also called Young’s modulus, measures the stiffness or rigidity of a material. PA66 GF30 has a relatively high elastic modulus, which ensures dimensional stability and avoids strain under load.
- Heat Deflection Temperature: The thermal deflection temperature is the start point and deform level of a material exposed to high temperatures. PA66 GF30 had a significant heat deflection temperature, which enhances its applications.
- Elongation at Break: Indicating the amount of flexibility a material possesses, or the stretchability, the amount of elongation at break seeks how much the material can stretch before breaking. Since PA66 GF30 has a relatively low elongation at break value, it can also preserve its form and not elongate due to stress.
- Chemical resistance: The exposure of PA66 GF30 to many chemicals is not a problem, thanks to its excellent chemical resistance.
Considering PA66 GF30’s mechanical properties and your application requirements, you should draw appropriate conclusions about its benefits and use them to improve your components’ quality, reliability, and durability.
Mechanical Strength and Stiffness of PA66 GF30
As a subject matter expert in the domain, I can confidently say that PA66 GF30 is a composite material with excellent mechanical strength and stiffness, making it suitable for more substantial applications. Furthermore, specific parameters like tensile strength, flexural modulus, heat deflection temperature, elongation at break, and chemical resistance must be examined when evaluating its mechanical properties.
- Tensile Strength: Including glass fibers within the nylon matrix for PA66 GF30 composite makes it an impressive material for tensile strength. The polymer encompasses the elongation required to not deform or break under tensile stresses, which is why this composite material is sought after for numerous performance-intensive applications.
- Flexural Modulus: The flexural modulus of PA66 GF30 can be measured to assess the material’s resistance to bending or flexing when loaded. With a high flexural modulus, this material ensures high dimensional changes and rigidity for efficient structural applications.
- Heat Deflection Temperature: Manufacturers would appreciate PA66 gf30’s high heat deflection temperature, which is ideal for high-pressure applications. This enables them to not worry about the structure losing dimensional integrity and stability due to overheating over time.
- Elongation at break: PA66 GF30 experiences a relatively low elongation at break, highlighting its capability to realize dimensional stability while resisting an elongation under stress. The degree of strain or load to which the material will be subjected to change its shape and structure is practically zero.
- Chemical Resistance: PA66 GF30 is excellently resistant to various chemicals, making it applicable in areas exposed to various chemical environments. Its chemical resistance also ensures its long durability over time and reliability in harsh conditions.
PA66 GF30 may be suitable for specific applications when assessing these mechanical characteristics. It possesses excellent mechanical strength, stiffness, heat deflection temperature, and chemical resistance, providing outstanding performance and reliability in various industrial applications.
Dimensional Stability and Rigidity
Dimensional stability and rigidity are crucial when evaluating a material’s suitability for specific applications. PA66 GF30’s mechanical properties contribute to its remarkable dimensional stability and rigidity, making it ideal for various industrial applications.
Mechanical Properties:
- High Modulus of Elasticity: PA66 GF30 exhibits a high modulus of elasticity, indicating its ability to resist deformation under stress and maintain its shape and structure even under significant load or strain.
- Low Coefficient of Thermal Expansion: The material has a relatively low coefficient of thermal expansion, which means it is less prone to expansion or contraction when exposed to temperature changes. This property ensures that PA66 GF30 retains its dimensional stability even in demanding thermal environments.
- High Stiffness: PA66 GF30 is known for its high stiffness, which provides excellent resistance to bending or flexing and contributes to its dimensional stability and rigidity.
Considering these mechanical properties, you can confidently assess PA66 GF30’s dimensional stability and rigidity for your specific application. Its exceptional modulus of elasticity, low coefficient of thermal expansion, and high stiffness ensure optimal performance and reliability in diverse industrial settings.
Resistance to Creep and Loads Over Long Periods
For the PA66 GF30 to be suitable for a particular application, it is essential to consider the rate of creep and the loads it can sustain over a long time. This is critical in its application in various industries. A better endurance against shape deformation under stress allows a material to be stable and maintain strength. Such simple properties allow for the PA66 GF30 to be used in various industrial applications where high dimensional stability is required over some time.
In determining the technical specifications of the composite materials, it’s essential to evaluate the following statistics:
- Creep or Wrinkling: The tendency of the polyamide composite polymer material to curl from one side is affected by compression, temperature, and time. Several polyamide composite polymer materials have specific low wrinkling rates, making them ideal for reinforced plastics.
- Mechanical Strength: The polyamide composite reinforced polymer was shown to have high stiffness and a very high modulus of elasticity, which makes it necessary to cause significant deformation or fracture under large loads.
- Thermal Expansion and Conductivity: The PA66 GF30 does not change in structure or mechanical properties significantly, regardless of the temperature range to which it is exposed. Its lower thermal expansion coefficient helps maintain stability within the structure irrespective of the temperature.
By considering these technical parameters and conducting a comprehensive evaluation, you can confidently determine the suitability of PA66 GF30 for your specific application, ensuring optimal performance and reliability.
How Does PA66 GF30 Perform Under Different Temperatures?

Because of its temperature range and operation benefits, PA66 GF30 can be used in various applications. Now, I will describe some of its temperature resistance and performance characteristics.
- Temperature Resistance: The PA66 GF30 maintains its mechanical properties and structural integrity when applied at high or low temperatures.
- Dimensional Stability: The material’s low thermal expansion coefficient lessens its temperature stability, allowing accurate functioning even under varying temperatures.
- High-Temperature Performance: PA66 GF30 also has remarkable heat resistance, ensuring that its appendages and even structures remain intact and functional when exposed to higher temperatures.
These remarks enable one to better appreciate and comprehend practical issues associated with the PA66 GF30 during the application process or even after its expected end of service.
Temperature Resistance of PA66 GF30
PA66 GF30 is an engineering plastic that exhibits good temperature performance. Its dimensional stability allows the material to perform well during temperature changes. The material can also withstand heat exposure while retaining its mechanical strength and structure even under high temperatures.
When comparing PA66 GF30 to other engineering plastics, one must be cautious of the differences between PA66 and PA6 and the differences with other reinforced GF plastics. PA66 GF30 excels in properties of high-temperature variation and excellent mechanical properties, which make it a reliable option in equipment requiring such high performance.
In the case of PA66 GF30, it is critical to adopt best practices in manufacturing, as this will guarantee the successful processing of it. This entails comprehending the technical data and specifications while dealing with the difficulties and solutions concerning processing this material. Considering all these, it will be possible to take advantage of the temperature-resistant and other beneficial features of PA66 GF30 when your application requires it for the best results.
Impact of Thermal Conditions on PA66 GF30
The capacity of PA66 GF30, a thermoplastic nylon with glass fiber stuffing, is conditioned by temperature. It helps to know the temperature conditions for the optimal use of this material in different applications. Some important conclusions concerning the effects of temperature on PA66 GF30 are listed below:
- High-Temperature Stability: PA66 GF30 nylon has high tensile strength, elongation at break, and compression set, which assist the polyamide to reach a high melting point, maximizing industry usage without affecting performance.
- Heat Distortion: Heat causes expansion in almost every compound, including PA66 GF30. To avoid potential performance problems caused by dimensional discrepancies in the configuration of interlocking parts, the thermal expansion coefficient (CTE) of PA66 GF30 should be factored into the design.
- Thermal Aging: PA66 GF30 thermoplastic’s mechanical disposition is likely to deteriorate if it is frequently subjected to heat over an extended period. A material property that ought to be checked is whether or not it can withstand extreme heat and still be useful. These properties include heat deformation, tensile strength, impact strength, and elongation at break.
- Heat Deflection Temperature (HDT): The HDT of PA66 GF30 indicates its capacity to withstand deformation under load in high-temperature environments. Understanding such loads aids in choosing the appropriate grade for the material and ensuring its application where high-temperature-induced dimensional change is critical.
To appreciate the effect of temperature on PA66 GF30, examining the technical data and specifications supplied by the manufacturers is helpful. These regulatory documents elaborate on the thermal properties of the materials, including HDT, CTE, and heat aging tests. As long as the guidelines for processing the materials are followed to the recommended requirements, PA66 GF30 can appropriately respond to the thermal demand of the specified application.
Performance in High-Temperature Environments
When working with PA66 G30, the ability to perform in high temperatures is a very important factor. As an engineering polymer, PA66 G30 has sound heat distortion at high temperatures. At this juncture, it is essential and appropriate to point out that reference should be made to technical documents and particulars provided by the manufacturers to ascertain whether the polymer is suitable for specific high-temperature applications. Usually, these data sheets contain a plethora of information relating to the material in question, such as set forth thermal properties, heat deflection temperature (HDT), coefficient of thermal expansion (CTE), and Heat aging performance. If directions regarding processing and thermal conditions required by the application are observed closely, then end products made with PA66 GF30 should be reliable and efficient. Technical resources, particularly those dealing with materials, should be consulted with a thorough analysis of the material when working in an environment with elevated temperatures.
Comparing PA66 GF30 with Other Engineering Plastics
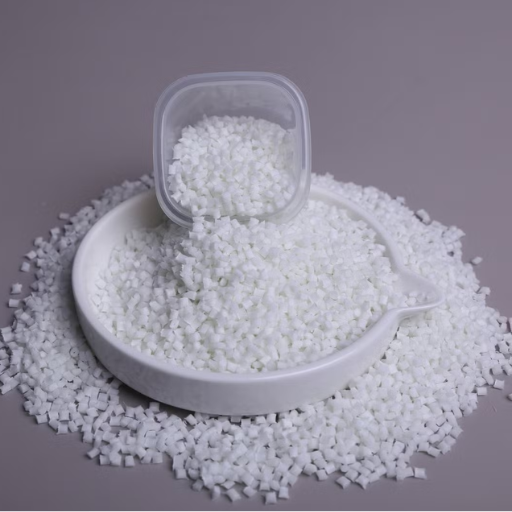
Several factors come into play when PA66 GF30 (30% glass fiber reinforced polyamide 66) is compared with other engineering plastics. Below are some of the highlights that one can focus on:
- Mechanical Strength: PA66 GF30 has considerable mechanical strength, especially in tensile strength, flexural strength, and impact resistance. Regarding these mechanical properties, GF30 outshines some engineering plastics, including PA6 and polyamide 6.
- Heat Resistance: PA66 GF30 can be classified as having good heat resistance because of its glass fiber reinforcement. Because of this characteristic, it is easy for PA66 GF30 to be exposed to high temperatures without substantial degradation of mechanical performance. Although it can vary greatly, in most situations, PA66 GF30 has more excellent thermal stability than some engineering plastics such as ABS (acrylonitrile butadiene styrene) or PC (polycarbonate).
- Chemical Resistance: One advantage of PA66 GF30 is its good chemical resistance, which enables it to be utilized in applications that interact with various solvents and chemicals. However, it is critical to note that the performance ability of PA66 GF30 is dependent on the exact chemical environment and concentration. In contrast, PVC (polyvinyl chloride) and other engineering plastics may have different chemical resistance characteristics.
- Processing Considerations: PA66 GF30’s glass fiber reinforcement predisposes it to specific post-processing techniques. Although injection molding is the most common, optimal fluid flow and minimal part defects can only be achieved if mold and processing conditions are adequately designed. Other engineering plastics might have to be molded or processed differently based on their make and characteristics.
However, when choosing from the PA66 GF30 or any other engineering plastic, the first target specifications are mechanical properties, load bearing, heat functionality, chemical effects, and other processing aspects. Sifting through technical resources, charting data, and testing would also inform which polymers would be best.
Differences Between PA66 and PA6
Polyamide 66 (PA66) and Polyamide 6 (PA6) are engineering thermoplastics in the same category, yet some differences are essential during the material selection process. Below are some differences between the two polyamides that one needs to be aware of.
- Chemical Structure: Chemically, PA66 is a polyamide consisting of hexamethylenediamine and adipic acid, giving it a linear structure. Caprolactam polymerization creates PA6, resulting in amide polymers with an asymmetric branched polymer structure.
- Mechanical Properties: First of all, PA66 has a higher strength than PA6 and high heat resistance. It has good impact resistance, withstands heat better, and can be used under conditions where stability and durability are required.
- Processing Conditions: PA66 differs from PA6 because it should be injected at a higher temperature and takes longer to cool. It is also more difficult to process because of its higher melt viscosity. Still, it is relatively more straightforward when the shape of the molds and processing conditions are set so that good fluid mechanics of flow are achieved, along with reduced part defects.
- Costs: PE66 performs better than PA6, but more complex manufacturing processes are employed, which also increases the cost.
For specific application needs, one should choose between PA66 and PA6 based on mechanical performance, heat function, chemical compatibility, and processing. It is advisable to research technical resources, evaluate data, and conduct further tests to establish which polymer best suits a particular need.
Comparison with Other Glass Fiber Reinforced Plastics
My specialization in glass fiber reinforced plastics (GFRPs) gives me more confidence while explaining comparisons involving PA66 GF30 and other GFRPs. The distinctively appealing mechanical characteristics and heat functionality of PA66 GF30 ensure that it serves various applications. Compared to other GFRPs, PA66 GF30 stands out because of its high strength-to-weight ratio, tremendous dimensional stability, and better resistance to chemical degradation. Moreover, PA66 GF30 can be utilized in electrical and electronics industries because it displays superb electrical insulation properties. Of course, cost, processing methods, and
the requirements of a particular application may play an essential role in selecting the GFRP type. Therefore, systematic reviews, assessment of technical documents, and expert interviewing are critical in choosing the best PPA solution for a particular case.
Why Choose PA66 GF30 for Your Application?
Selecting PA66 GF30 for your application has several advantages:
- Outstanding Mechanical Performance: It is evident that PA66 GF30 has exceptional strength and weight characteristics; in other words, it is suited for use in circumstances with rigorous weight constraints yet requires durable elements.
- Excellent Resistance to Deformation: PA66 GF30 is generally known to have outstanding resistance to dimensional changes; even under challenging conditions, the likelihood of twisting or bending is considerably lower.
- Improved Chemical Resistance: Compared to PA66 GF30, it is crystal clear that the latter is superior to all other GFPRs; in particular, its resistance against chemical assault is remarkable.
- Excellent Electric Insulation: PA66 GF30 has remarkable electrical insulation characteristics, making it appropriate for electrical and electronic components requiring reliable insulation.
When you select PA66 GF30 for your application, consider that PA66 technical data and specifications are part of your requirements. Other aspects should also be considered, such as the cost, how it will be processed, and the uses to which it will be put. You could do so by conducting proper research, asking experts, and testing the technical parameters to ensure that your application meets the performance criteria but at a reasonable cost.
Processing Techniques for PA66 GF30
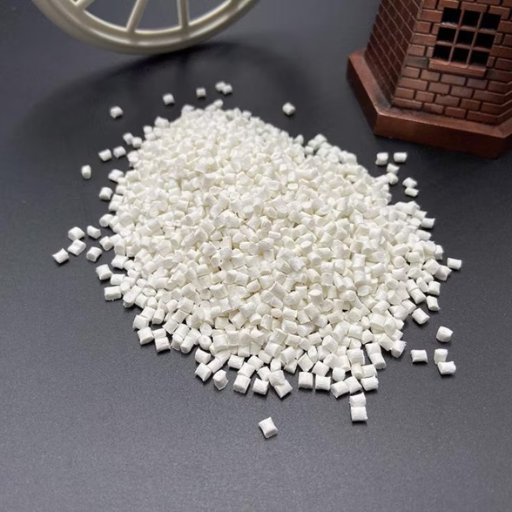
One should consider a few critical facts to achieve the best results when working with PA66 GF30. They are as follows:
- Parameters for Injection Molding: The parameters must be controlled accurately to achieve the appropriate mechanical and dimensional characteristics. The most important ones are melt temperature, injection pressure, speed, and cooling time.
- Venting and Mold Design: It is vital to create a mold for PA66 GF30 to prevent sink marks, warpages, and voids from occurring. This is also essential for proper ventilation, which vents air and gases.
- Material Drying: PA66 GF30 is classified as HYGROSCOPIC, meaning it draws moisture from the atmosphere. Therefore, proper drying of the material before processing is essential. This will help avoid defects in the surface and loss of the product’s mechanical properties.
- Melt Temperature and Residence Time: It is crucial to manage and control bonded parts’ melt temperature and residence time to prevent them from degrading. Too much exposure to heat can result in thermal degradation, lowering the mechanical performance of the bonded material and, subsequently, its performance.
- Gate design and placement: If the gate’s configuration and position are appropriate, smooth filling and the risk of blush can be maximally avoided. The gate’s location should be strategically set to reduce visual defects in the molding and achieve optimum quality in the part itself.
You need to remember that the recommended processing conditions for PA66 GF30 will likely change with the equipment used, the geometry of the component or part, and the requirements of its end use. The potential needs applying sufficient research, asking experts, and testing to provide the required performance while considering the cost, processing possibilities, and the application.
Best Practices in Manufacturing with PA66 GF30
Producing parts using polyamide PA66 GF30 (30% fiberglass reinforced polyamide) should account for numerous elements to maintain the best process and part quality. The following are some helpful guidelines which should always be paid heed to:
- Material Handling: PA66 GF30 should always be protected from moisture, especially during storage and movement, as moisture can affect its mechanical properties. Driers and other dehumidifying equipment would be helpful if necessary.
- Machine Selection: It is crucial to employ the right injection molding machine for PA66 GF30, which has the necessary melting capacity and temperature control.
- Melt Temperature and Residence Time: As for the melt temperature of PA66 GF30, the recommended range should be adhered to to avoid thermal degradation; usually, this is around making the temperature about 280 ̊C to 300 ̊C. Residence time is essential both for ensuring heat levels are controlled and reducing the amount of excessive heat encountered.
- Injection Speed and Pressure: By controlling both injection speed rate and injection pressure, injection parts should be optimized for uniform filling and lower part defects. This would also apply to this low-filled resin, PA66 GF30, due to its higher viscosity than standard resin.
- Gate Design and Location: The perfect gate design would ensure minimal visual defects by controlling the smooth flow at the appropriate location of the gates, considering the geometry of the part and mold design. Suitable gates for PA66 GF30 include edge gates, submarine gates, and fan gates.
- Cooling and Mold Temperature: Proper cooling devices and keeping the mold temperature are essential for ensuring dimensional accuracy and minimizing cycle times. For most applications, this is approximately 60–80 °C.
Remember that application requirements may be more specialized, so seek the advice of material suppliers, mold designers, and processing experts for specific guidance. Adequate testing and validation can assure the performance and quality of PA66 GF30 parts.
Technical Data and Specifications
A few technical requirements must be met to finish the injection molding process for PA66 GF30. These technical requirements and specifications provided below will assist in achieving better results:
- Material Properties: PA66 GF30 is a nylon composite reinforced with glass fiber. It exhibits enhanced mechanical strength, rigidness, and elevated temperature tolerance. The mecha properties of these products differ depending on the grade and processing methods used.
- Processing Temperature: The ideal processing temperature for PA66 GF30 is 250-280 degrees Celsius. However, it is recommended that the specific recommendations provided by the suppliers be checked for clarity on temperature boundaries and due diligence testing be carried out.
- Injection Speed and Pressure: Since PA66 GF30’s viscosity is greater than that of resin containing no fillers, injection speeds and pressures would need to be increased. This would assist the melted matter in reaching and filling the cavities of the molds.
- Gate Design and Location: To allow sufficient flow and minimize cosmetic deficiencies, careful design and placement of the parts, including the type of gates, edge gates, submarine gates, and fan gates, are necessary. The decision on the location of the gate should be made after analyzing the geometry of the part and the layout of the mold.
- Cooling and Mold Temperature: Adequate and organized cooling procedures and mold temperature control are necessary to achieve the desired dimensions and reduce the cycle time. The Formation temperature for the PA66 GF30 mold is generally between 60 and 80 degrees Celsius.
It should be pointed out that the data presented above are just essential particulars. For particular recommendations, it is better to contact material suppliers directly, mold design engineers, or experts in molding, who can provide more specific information about your application’s requirements. Further extensive testing and validation are necessary to realize the expected performance and quality of PA66 GF30 parts.
Challenges and Solutions in Processing PA66 GF30
The unique features of PA66 GF30 enhance diversions during production and allow for successful molding once specific challenges are overcome. The following are among the broadest challenges faced.
- Fibers Alignment: Incorporating glass fibers into PA66 GF30 prompted the issue of fiber alignment, resulting in differential mechanical properties in all directions or anisotropy. These challenges can be manageable by improving the mold design, gate configuration, and process parameters.
- Deformation and Reduction: The tempered state of PA66 and thermoplastic glass fiber composite deform with heat and retracts more than unfilled resin. To avoid these issues, tension-controlling devices, mold temperature, and component shape must be as required.
- Filling and Flow of The Mold: Due to the increase in viscosity of the media, ensuring that all molds are filled to the brim and a homogeneous flow throughout is hard to achieve. Fixing the injection rate, amount of force exerted, and the gate’s size and shape are some adjustments with this difficulty.
As a better outcome, followed by high-quality parts, understanding these specifications, everyday occurrences, and the processing challenges of PA66 GF30 is key to being successful as a manufacturer in this industry.
Frequently Asked Questions (FAQ)
Q: What is PA66 GF30?
A: PA66 GF30 is a type of polyamide, also known as nylon 66, reinforced with 30% glass fibers. This material is widely recognized for its excellent mechanical properties and is commonly used in applications requiring high strength and durability.
Q: Why is PA66 GF30 considered one of the strongest glass fiber-reinforced plastics?
A: PA66 GF30 is among the strongest glass fiber-reinforced plastics due to its outstanding mechanical properties, high tensile strength, excellent creep resistance, and reduced moisture absorption. These properties make it suitable for demanding applications with critical strength and stability.
Q: What are the electrical properties of PA66 GF30?
A: PA66 GF30 exhibits good electrical insulation properties, which makes it suitable for electrical and electronic applications. Its ability to maintain performance when exposed to high temperatures further enhances its utility in electrical components.
Q: How does PA66 GF30 compare to other used plastics in terms of strength?
A: Compared to other plastics like PA6 or non-reinforced polyamides, PA66 GF30 offers superior strength and stiffness. Its glass fiber reinforcement contributes to its excellent mechanical performance, making it more suitable for high-stress applications.
Q: Can PA66 GF30 be used for sliding applications?
A: PA66 GF30 is less suitable for sliding applications due to its high glass fiber content, which tends to have a marked abrasive effect on mating surfaces. Alternative materials might be more appropriate for applications requiring low friction.
Q: What are some typical applications of PA66 GF30?
A: Common applications of PA66 GF30 include automotive components, industrial machinery parts, and electrical housings. Its excellent strength and thermal stability make it ideal for use in environments where other materials may fail.
Q: Who are the leading manufacturers of PA66 GF30?
A: Leading manufacturers of PA66 GF30 include Ensinger, which offers products like Tecamid® 66 GF30, and other companies producing similar reinforced polyamides such as Sustamid® 66 and Zellamid® 250.
Q: What is the chemical resistance of PA66 GF30?
A: PA66 GF30 exhibits good chemical resistance, particularly against oils and greases, making it suitable for use in environments where chemical exposure is a factor. However, its performance should be verified for specific chemical exposures.
Q: How does moisture affect PA66 GF30?
A: PA66 GF30 has a reduced moisture absorption rate compared to other polyamides like PA6, which enhances its dimensional stability and mechanical performance, especially when exposed to high humidity or wet conditions.
Q: How does PA66 GF30 perform in molding processes?
A: PA66 GF30 is well-suited for injection molding due to its excellent flow properties and dimensional stability, allowing manufacturers to efficiently produce complex and precise components.